We’ve reviewed a novel, vendor-agnostic pre-concentration screening test in part one and explained a comprehensive five-step pre-concentration evaluation in part two…now for part three in the three-part series with SRK Consulting (Canada) Inc’s Adrian Dance (Principal Metallurgist) and Bob McCarthy (Principal Consultant)
SRK Consulting’s Adrian Dance and Bob McCarthy have devoted years to ensuring the mining industry can make informed decisions about preconcentration within their flowsheets and are now able to screen the opportunities quickly, cost-effectively and without vendor prejudice.
“We have been carrying out the different parts of the five-step evaluation process over the years, refining them independently and sometimes together,” McCarthy tells IM. “It is only now that we can present them all in a holistic way.”
This five-step process – which includes heterogeneity analyses; “size the prize” economics; laboratory test work that involves X-ray Transmission (XRT) based sensor technology; mine planning; and mine economics – has been deliberately designed to allow mining companies to pause at the end of each phase to re-evaluate if there is a strong enough case to continue with a preconcentration investigation.

The importance of such an approach has grown in recent years as more projects that are “grade-challenged” or metallurgically complex are being considered for exploitation by mining companies as the demand for metal increases worldwide.
Sensing this (pun intended), sorting and sensing manufacturers have been on the mining charm offensive, proclaiming the benefits of their technology – benefits that include cost reductions, improved metallurgical recoveries, rationalised use of energy and water, and more.
These market dynamics have created a void that SRK is looking to fill by providing the tools for both sides to assess the options and carry out informed decision making on which routes to pursue.
“We were concerned that the manufacturers didn’t have the background needed to understand the mining industry’s requirements,” Dance said. “At the same time, mining companies had difficult projects and deposits where they saw pre-concentration potential but didn’t know where to initially go to explore that potential.
“We saw a space for industry representatives like ourselves at SRK to bridge that divide.”
The independent testing that SRK has been able to offer for the last six or so months through its partnership with Base Metallurgical Labs (BML) in British Columbia was the final piece of the puzzle in establishing this nowestablished five-step process.
Able to not only indicate pre-concentration amenability but also provide key inputs into the pre-concentration strategy selection and evaluation, this has been employed for some 36 samples (close to 2,000 particles) being tested using the XRT unit situated in BML’s facility in Western Canada.
Demystifying the tech
While this XRT testing may have only recently become available to SRK and BML customers, the outcomes of SRK’s pre-concentration evaluation have been described to investors and stakeholders trawling through NI 43-101 reports up to the prefeasibility study (PFS) level for some time now. Various parts of the five-step evaluation have come into sections on metallurgical test work, mineral reserves, mining methods, costs and economics.
“Where the results feature is tied to what study stage the company is at and where people feel comfortable with pre-concentration,” McCarthy explains.
Providing comfort to mining companies and their investors is always difficult when examining any new flowsheet addition, hence the reason why many companies are initially pursuing pre-concentration or ore sorting in a ‘recovering ore out of waste’ scenario from material already deemed to be waste and having no economic value.
As a result, SRK has been very deliberate in the protocols it is pursuing.
Dance explains: “Because there is still a perceived ‘magical’ nature to preconcentration in that it can provide reserve upgrades and higher recoveries, we need to do more detailed evaluations at a preliminary economic assessment or PFS level than would be expected for other types of processing technology.”
For instance, the company is currently engaged on a gold operation where it has tested upwards of 22 samples (1,320 particles) for validation. “At this level of study, if you were working on comminution or leaching, the same process validation would be carried out with two or three tests,” Dance said.
McCarthy added: “We firmly believe that this five-step evaluation will allow people to sign off, at least at a PFS level, on whether pre-concentration is a viable route for them to take. Our process will prove this through testing and pulling different economic levers in the economic evaluation to quickly see where the value is, and where it isn’t.
“If pre-concentration is viable, you would then likely see clients moving on to performance testing with some of the sensing/sorting vendors at the feasibility study stage.”
Welcoming the independence
Those who understand the pre-concentration space have welcomed the involvement of SRK through its five-step process and, in particular, have highlighted the industry need for standardised and independent testing.
“They see where we are inserting ourselves into stages of the client and vendor relationship,” Dance said. “In no way are we competing with vendors – we are not suggesting we have the expertise they have. Rather, we are looking at the characteristics and amenability elements for the vendors to then truly apply their expertise, knowledge and sensor selection understanding.”
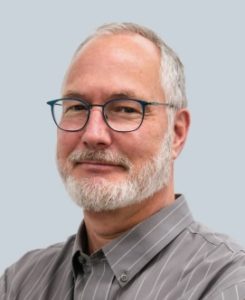
At the same time, Dance and McCarthy are looking to arm mining companies with relevant knowledge about pre-concentration principles, where the process could provide a grade uplift and what losses might be associated with the implementation. This is being done through gaining a better understand of their orebody through the testing.
It should result in mining companies providing a more representative sample to the pre-concentration vendors for the performance testing many of them offer. “Mining companies can then understand these pilot test results more broadly and ask more questions, if needed,” Dance said. At the same time, the vendors have a ‘pre-qualification’ check in hand: they would know from the SRK process if there is a strong basis for carrying out the performance test in the first place.
And, of course, SRK can get involved after the five steps are complete, carrying out small-scale work and integrating these results with the larger
scale performance testing that could eventually underpin a flowsheet developed by a third-party engineering company.
“We view pre-concentration as another aspect of geometallurgy that needs to be interrogated just like comminution and flotation,” Dance said.
The future focus
It is potential changes to both of those processes that could have positive implications for pre-concentration in the mining sector.
“We’re now seeing more flowsheets designed with a multi-stage comminution flowsheet that, at every stage, asks: ‘do I need to process the oversize material again?’” Dance said. “There is an opportunity for the right sensors to answer those questions. That is being highlighted in the design of some of this technology; some newer ore sorting units are reminiscent of cone crushers in size and shape, which means they can be inserted into this flowsheet with ease.
And, of course, some pre-concentration-focused companies have gone upstream of the plant to the pit to provide these readings: an area Dance sees as representing the future.
“Heterogeneity is better preserved the further upstream of the plant you go, so it is obvious to think that pre-concentration technology – which feeds off this heterogeneity – should be placed here,” he said. “The issue comes with getting a representative sample to test – whether that is a shovel load, or the equivalent of what a 200-t payload truck can carry. Ultimately the mining industry is at a ‘prove it’ stage when it comes to pre-concentration technology. The mining companies want to see results on paper or on a screen before they sign off on this technology and process. At the scale of a truck or shovel, this is very challenging.”
McCarthy added: “The Heterogeneity and Scale analysis we are doing in step one of the evaluation will identify some of these opportunities within the selective mining unit sizing, but it is still early days on factoring that into sorting at a truck or bucket scale.”
This work will require closer examination of the drill core than the typical 1-m assayed intervals, as well as a way to estimate the level of mixing that occurs between vertical blast holes, post-blasting, post-loading and post-conveying.
This comprehensive plan is broadening too, factoring in more than just economics.
For instance, SRK has made a case for carrying out the same sizing and XRT analysis included in the five-step evaluation for mill pebbles – which can represent up to 30% of the entire plant feed in some cases – to assess their true value.
This obviously has a cost benefit, as well as an energy benefit – avoiding recirculation of pebbles avoids excess energy use. This same testing is indicating there could be further energy benefits to be had by using preconcentration, too.
In addition, “We have recently expanded our testing protocol to now measure specific energy requirements of the concentrated material compared with the original feed,” Dance said. “This has shown (at times) a softening effect of pre-concentration that can produce measurable savings in power.”
And the impacts on water and energy use are another avenue that could come into the ‘size the prize’ economics McCarthy uses in step two of the five-step evaluation process. “There is no reason to think this could not be included in the analysis in the future; all we would need are the metrics for the existing proposed operation – the amount of water and energy used for the number of tonnes in the mill feed,” he said. “It will then just be a simple case of amending the two inputs based on the pre-concentration work.”
Against a backdrop of falling grades, increasing metallurgical complexity and perceived future demand for commodities, the pre-concentration question needs to be asked by all companies.
For more information on the XRT pre-concentration screening test SRK and Base Metallurgical Labs can provide, as well as the five-step evaluation process for pre-concentration amenability, click the link here