Every train, industrial, or transportation vehicle needs a unique traction powertrain for operation, with ABB, through its Traction division, holding a complete and flexible product portfolio that, it says, allows it to build the perfect electrification solution for operators to transition businesses to more sustainable and lower cost operations.
Each of these solutions can be tailored to customer requirements and the operating conditions of each vehicle that it powers, enabling maximum energy efficiency, zero carbon emissions and high reliability.
The company is able to leverage high-tech e-mobility and rail system traction converters, energy storage systems and electric vehicle charging solutions as part of its offering, complementing this with enhanced expertise to help accelerate the transition to all-electric operations.
One project where its impact has been felt is at Nuh Cement in Turkey where ABB is working jointly with the company to convert 10 mainly Euclid/Hitachi dump trucks with an average 160 ton capacity, which have completed their 30-year service life, from diesel engine power to electric.
This is one of the first mining truck battery conversion projects of its kind in the world and will be discussed in more detail during a presentation at The Electric Mine 2024.
Ahead of the event, taking place at the Crown Perth Complex, on May 21-23, we spoke with Fabiana Cavalcante, Head of Mobile e-Power at ABB, to find out more about the offering.
IM: ABB’s Traction division is working within a very competitive landscape when it comes to e-mobility in mining. What would you say are your unique selling points to the industry?
FC: We bring over 130 years of experience in mining electrification, combined with extensive expertise in electrification and charging infrastructure for cars, buses and trucks. This allows us to extend our capabilities to the final piece of the puzzle: electrifying mobile equipment.
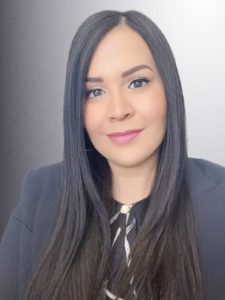
Our journey began by utilising our unique knowledge in rail propulsion systems and adapting it to the harsh environment of mining. Our roots in electrifying the Swiss railway network over a century ago have established us as leaders in sustainable transportation solutions. We have translated this experience to increase energy efficiency, reliability and reduce emissions across rail networks, electric buses and other heavy vehicles. The building blocks of the technology are similar, making for a smooth transition.
Besides this, what truly sets us apart is our capacity to execute customised customer projects. Battery-electric propulsion requires more personalisation compared to diesel, and our history as an independent supplier has equipped us with the skills, mindset and a perfect portfolio of proven base components to adapt quickly and in larger quantities than any other company.
IM: You work with multiple OEMs and solution providers across the globe looking to electrify their operations. Are most of these companies looking to electrify their offerings during a similar timeframe?
FC: Many mining operators have ambitious sustainability targets, aiming to reduce their Scope 1 and 2 emissions by at least 30% by 2030. By 2050, many operators aim to achieve net-zero emissions, and the only path to that is by electrifying their mining vehicle fleets. If every truck in every mine were electrified, we could remove 198,000 tons of CO2 from the atmosphere each day. Mining operators and OEMs recognise the potential to minimise their carbon footprint, and while this transition won’t happen overnight, we’re excited to partner with them and guide them on their electric journey.
IM: How often are you interacting directly with the operators during these types of projects? At this stage, is it often a collaboration between ABB, the OEM and the client?
FC: The level of interaction varies from project to project. In some cases, we have limited direct engagement with the mine operator, while in others, we are heavily involved. A recent example is our collaboration with Boliden and Epiroc, where we worked together to create the first battery-electric trolley truck system for underground mining. This close partnership was crucial to bringing this innovative project to life.
IM: In this regard, how does your work with Nuh Cement on converting its diesel powered fleet to electric power stand out from the work you normally carry out? Why is Nuh Cement able to collaborate directly with ABB on such a project?
FC: Nuh Cement approached us with the goal of converting their existing mining fleet of Euclid/Hitachi dump trucks to electric power and we officially began the project in 2022. We have vast experience in retrofitting vehicles for the rail business and we followed the same approach and procedures for the haul trucks.
The steep ramps with up to 20% gradient required us to pay close attention to ensure that the electric trucks could meet the expected performance and efficiency levels. This involved intense collaboration between both parties to translate simulations into practical, real-world solutions. Working closely with Nuh Cement, we tailored our solutions to fit their specific operational requirements and made sure our technologies aligned with their vision for a sustainable future. We hope many more mine operators will soon start to electrify their fleet and we’re excited to closely partner with them throughout their journey.
IM: Are you able to provide a sneak preview of what you will present at The Electric Mine 2024 in Perth about the Nuh Cement project? How has this project advanced since it was announced back in 2022?
FC: I’m excited to share the results of our groundbreaking collaboration with Nuh Cement at the event. Our partnership led to the successful electrification of a haul truck, demonstrating ABB’s ability to retrofit diesel-powered vehicles into fully electric ones – a milestone with significant implications for the mining industry. This transformation of a 30-year-old vehicle into a net-zero haul truck sets a new standard for sustainable mining practices worldwide.
Additionally, attendees will hear from Nuh Cement’s CEO, Kamil Gökhan Bozkurt, who will provide insights into this key project.
IM: In addition to what you have already discussed above, what can attendees of The Electric Mine 2024 look forward to hearing about next month?
FC: I encourage everyone to visit our team at booth 58 during the conference. Attendees will have the chance to explore our latest technology and innovations, including a preview of our new energy storage system, which offers exceptional lifespan, power and safety. We look forward to seeing you all there!
ABB is a Gold Sponsor of The Electric Mine 2024, with the company having a major indoor display in the exhibition hall. Fabiana Cavalcante will be on stage at the event presenting, ‘Powering progress: ABB and Nuh Cement’s zero emission dump truck’ during Day 1 of the event. Find out more about The Electric Mine 2024 by going to www.theelectricmine.com