Finding the sustainable edge through innovation
Sustainability is one of the most central themes facing today’s mining industry. It is simply a fact that mining and mineral processing places heavy demands on both energy consumption and water usage. It also needs to deal with the safe handling of by-products from the mining process and the disposal of waste such as equipment, liners and components that are used up or damaged from the daily wear and tear they encounter.
The world needs minerals as it pushes towards electrification and a more sustainable future with nickel, copper and lithium, among others, playing important roles in the energy transition. As global demand grows, miners are forced to increase production to keep pace, increasing the environmental pressure. Many sites struggle to find the right balance between increasing production while continuing to meet their environmental commitments and goals. In some cases, improving their sustainability agenda and execution has become the top priority, with governments insisting on improvements as a licence to operate. Failure to meet new requirements can mean penalties and, in some cases, suspension of activities or even closure of a site until regulations are met or exceeded.
But where to start?
With all these pressures to improve their performance in managing resources and waste, sites are looking at their operations and asking themselves where to start. Investing in newer more energy-efficient equipment is one option but can come with a high capital cost that may deter some sites from investing. Finding ways to improve existing operations can often be a good place to begin. Recent innovations in spare and wear parts, recycling and even upgrades to specific equipment can all afford a lower cost barrier to realising substantial improvements.
Crushing – optimisation and innovation for longer life
Finding areas of development in the crushing process is a great place to improve efficiency and sustainability. For example, regarding wear parts, a chamber optimisation program can identify areas for improvement. Chamber alloy selection and customisation of profiles in one or more crushing stages can contribute to higher production rates, crushing efficiency, safety and reduced downtime. Optimisation can also result in up to 30% reduced energy consumption and a reduction in liners consumed, allowing sites to move closer to their environmental targets.
As working wears require regular change-outs, thinking beyond automatically reordering the same liners can also bring significant benefits. MX for cones, an innovative solution that is specially designed for large cone crushers, is a great example of a high-wear solution. Wear life can be up to double with the use of MX for cones over more standard wear parts. This results in fewer new liners needing to be produced, less raw materials used and reduced environmental impact from logistics. MX for cones is also 100% recyclable.
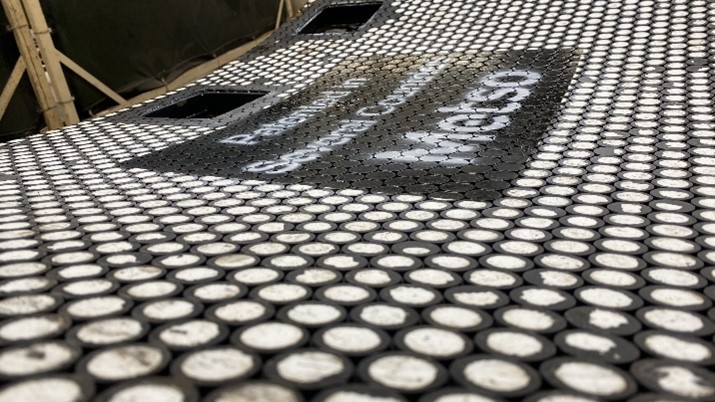
In addition to working wears, protective wears are an honourable mention. Selecting long-lasting protective wear parts, such as Poly-Cer, can increase wear life by up to multiple times. Maintenance schedules can be better aligned with working wears and risk exposure is minimised with fewer change-outs. As fewer liners are needed due to the improved wear life, more sustainable operations are supported throughout the supply chain.
Grinding – shifting to a circular economy with mill lining recycling
Dealing with worn mill liners has been a significant challenge for many mine sites and concentrator plants striving to reduce their environmental impacts. The process of changing out the linings on one or several mills over the course of a year can result in thousands of tonnes of worn linings that typically end up in already overloaded landfill sites.
To address this problem, Metso offers an innovative recycling service for worn mill liners for mine sites in Europe, South America and, in the near future, to North American customers. This first-of-its-kind service is designed to recycle and create value from used mill liners on an industrial scale.
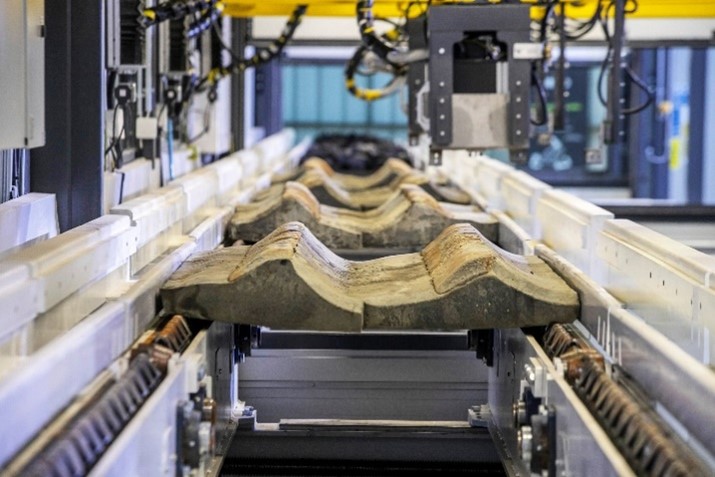
By breaking the bond between rubber and metal components, all composite mill liners, such as Megaliner™ and Poly-Met™ as well as rubber liners, can be processed. Instead of being sent to a landfill, the different liner components can be recycled or reused in the most optimal way.
As many mine sites have ambitious agendas and are implementing long-term strategies for decarbonisation with a commitment to net zero in their operations, this service can help meet that need and offers a way to reduce CO2 emissions and improve environmental efficiency.
High-performing and long-lasting mill liners go hand in hand with both economic and environmental benefits, leading to a more efficient operation. For instance, with an optimised design they can last longer and use less material. The liners, or even the entire grinding circuit, can be optimised for increased efficiency and reduced energy consumption.
One example is Metso’s recent mill lining innovation, Skega™ Life rubber, which increases the wear life by up to 25%. This reduces waste and means less production, transportation and replacement of products.
Flotation – finding the right mix for reduced CO2 emissions
Launched in 2006, FloatForce® has set the standard for efficient flotation mixing mechanisms in the industry, but recent R&D breakthroughs have unveiled new ways to enhance performance and sustainability. With FloatForce+, Metso offers a plug-and-play solution that maximises metallurgical recovery, boosts pumping efficiency, and reduces energy consumption, helping you recover valuable materials and increase revenue with the “right mix”.
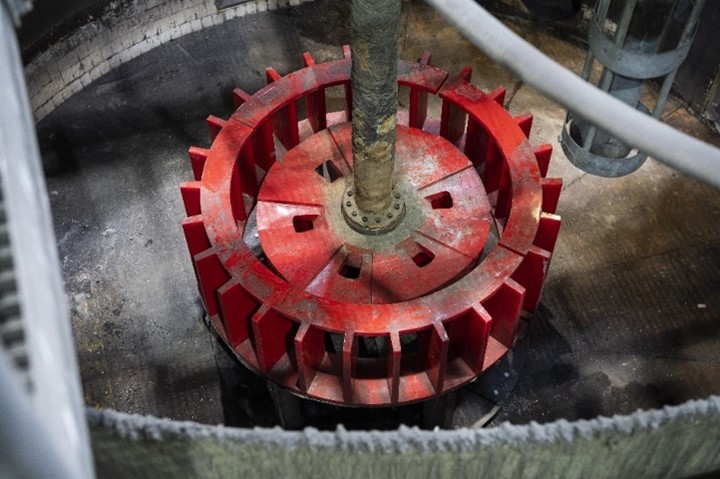
This upgrade is part of Metso’s Planet Positive offering and aligns with our goals by optimising manufacturing materials and lowering CO2 emissions. It integrates seamlessly with digital solutions, enabling you to track energy consumption, recoveries and maintenance planning.
When 2+2 can equal 5
Taking a closer look at a particular process stage or even a single piece of equipment within an operating circuit can bring opportunities to improve energy and water use and drive down waste destined for landfills. In many cases making a simple change, such as trying out a new design or material, or examining the payback of upgrading a crusher, float cell or filter with the latest technology may bring immediate gains. Combining several improvements across a flowsheet can multiply or even exponentially increase the effect, leading to greater improvement than the sum of the individual contributions. Finding a trusted supplier and partner at the forefront of innovation and pushing the boundaries with new solutions can often be worth its weight in gold when it comes to meeting your targets.
For more ideas and inspiration, explore Metso’s full aftermarket offering here: Your #1 service partner from pit to port