After Glenn Brearey and Mathew Rigby explain the WearVue® concept, it is hard not to ask: ‘What’s the catch?’ The visual indicator system the pair are promoting – and now installing on truck trays in Western Australia – is both simplistic and ingenious. It makes so much sense for an industry calling out for more affordable wear monitoring solutions.
“Mat and I come from hands-on backgrounds in mining and maintenance, and WearVue was born out of our frustration with the traditional approach to wear monitoring,” Brearey, one of the founders of the company with Rigby, told IM. “The ADHD innovation factor helped drive our thinking, simplify the problem, make the solution visual and remove the complexity that slows things down.”
At its core, WearVue is a patented colour-coded system that showcases the level of wear on a piece of equipment through visual “indicators”. The three variants – green for “good to go”, yellow for “plan maintenance” and red for “act now” – are easy to comprehend and can be observed visually by maintenance technicians.
“We have seen that the current wear measurement systems on the market are inaccessible to non-specialists and rely on expert interpretation,” Brearey said. This makes it difficult for those at the front line to make accurate assessments of wear with mainly sensor-based solutions.
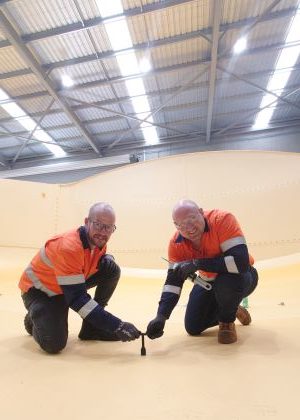
On top of this system accessibility issue, the current maintenance status quo is putting these same workers in danger, with stress, fatigue and risk of injuries part and parcel of the normal inspection process.
According to the National Institute for Occupational Safety and Health, 48% of mining maintenance fatalities happen during inspections: a statistic that Brearey and Rigby have no pleasure in highlighting.
“The industry needs a solution that eliminates the need for hazardous manual inspections, reducing the likelihood of human error and keeping workers out of the line of fire,” the company states in one of its promotional videos.
This is where WearVue comes in.
Available as either pigmented plastics, epoxy/polyurethane resins, or embedded markers, these indicators can show progressive wear over time, with a quoted accuracy of 0.1 mm.
“We see this as a disruptive technology in the way that it has a very low entry point from a cost perspective, is scalable – you can progress from visual inspections through to AI-backed analysis – and is accessible for all,” Brearey said. “These same indicators can be fluorescent too, meaning that analysis can take place any time.”
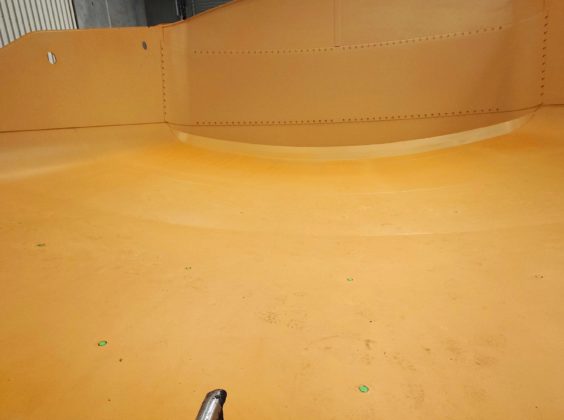
Brearey’s disruption comment is also backed up by the numbers WearVue states in its technical document.
It achieved vendor status with BHP – the world’s biggest miner – within three months of operation setup. Alongside this, it has established a partnership with Indigenous-owned company Maali Mechanical Services to help service these orders.
When IM spoke with the WearVue founders the pair were coming off their first indicator fitting – some 15-20 indicators on board a Komatsu 930E-5 haul truck tray about to go into an operation owned by a Tier One miner. This was part of an order to install the WearVue indicators on four 930E-5 truck trays.
The company assessed wear patterns using site-issued wear rates and operational data to determine the optimal placement of these indicators, saying both the number of indicators used and position of said indicators varies from site to site.
The focus, for now, is on truck trays. The company also has renders for indicators fitted on heavy off-road tyres, wear plates and chutes, conveyor rollers and drive belts, and automotive braking systems in its technical document. Brearey and Rigby also talk up ground engaging tool wear monitoring as another obvious area to expand into.
Rigby offers up an example of how the indicators could act in a conveyor belt roller wear scenario: “We can tune the yellow section of the wear indicator based on the lead time that it takes to get that new replacement product through to site. So, for example, if it takes them six weeks for this, we can analyse the data to manufacture an indicator with a yellow layer that reflects that.
“As soon as the team or, it could be the computer, sees that yellow layer appear, a command to place an order and book that roller in for maintenance in six weeks’ time could be made.”
This could reduce the inventory holdings for mine sites, as well as better align maintenance regimes with actual wear performance.
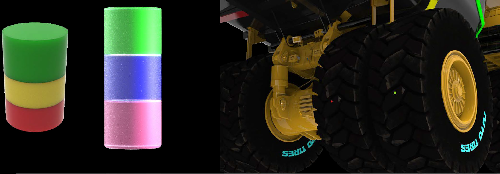
It’s easy to, therefore, see why a company like BHP may have fast tracked the approval process to get WearVue on its approved vendor list – not only could it optimise inventory management; it could also allow the company to easily benchmark how ‘hard wearing’ the solutions it is buying are, as well as reduce its emissions by only replacing equipment/components when required.
The industry may not want more disruption with the growing need to decarbonise operations and hit their net-zero targets, but it is likely to be much more receptive to the upheaval WearVue is aiming for.
“We’re not asking operations to remove or add people to take advantage of our solution,” Brearey says. “We’re saying we can use the same people and remove them from harm’s way by using our system. At the same time, you can see mine managers walking past spent GET that has red indicators all over it knowing that they have used it to their full capacity; that it is all worn out.
“We’re empowering everyone on the mine site with what we have to offer with WearVue.”