Many underground mines, despite billions in investment, continue to fall short of their development and production goals, with production shortfalls on a quarterly, six-month and annual basis regularly observed by the investment community.
MasterMined Innovation, a company focused on applying innovation to accelerate the future of mining, reasons that a lot of these performance failures are tied to mine planning. “This is often spreadsheet-based, with anticipated bottlenecks either misunderstood or overlooked.”
Against this backdrop, the most common fix is ‘Work harder’, the company says.
FlowCycle, developed by MasterMined Innovation and built for both mine development and production contexts, is looking to change this.
A systemised mine performance uplift approach with the potential to deliver immediate results, FlowCycle builds a foundation for long-term transformation, according to Tony Sprague, founder and CEO of MasterMined.
“Grounded in Lean thinking, the Theory of Constraints and decades of operational insight, FlowCycle helps mine teams see what’s really holding them back – and provides the tools and structure to break through,” he added.
The FlowCycle system combines site performance data, frontline insight and calibrated discrete-event simulation modelling to visualise how mine development and production actually flow — and where they break down.
MasterMined says this method allows site teams to:
- Identify the true constraint in their mine system — not just surface symptoms;
- Focus improvement efforts on the bottlenecks that matter most; and
- Build a structured uplift roadmap backed by data, systems thinking and frontline input.
Sprague said: “FlowCycle reveals your real constraint — then helps you fix it with structure, not hope.”
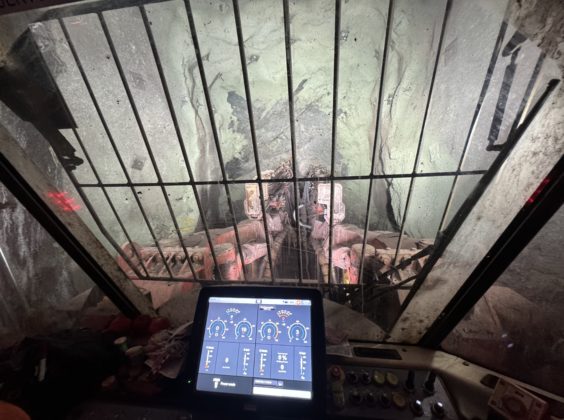
MasterMined has already tested elements of FlowCycle across various underground operations, with clear benefits observed in development performance, equipment utilisation and shift efficiency, it says.
The company is currently working with multiple mining companies and several major mining fleet OEMs, all of whom recognise the game-changing potential of FlowCycle to uplift mine performance at both a system and operational level, MasterMined added.
All of this is achieved by using a constraint-based approach, which focuses the mine’s attention on its real production constraint: aligning teams and resources.
A custom-built mine simulation model helps test hypotheses, quantify improvement potential and build confidence, with MasterMined working side-by-side with supervisors, engineers and operators to design and implement changes, ensuring the team can take the recommended actions.
“FlowCycle is not a one-off initiative,” the company says. “It’s a repeatable system enabling sustained performance uplift.”
Sprague says the system is able to integrate with existing mine planning and operational tools to enhance – not replace – current systems.
“It also lays the groundwork for successful technology adoption, supporting initiatives like jumbo automation, ground support innovations and remote charge-up – not as isolated pilots, but as part of a coherent, flow-based operating system,” he added.
Based on simulations and expert application of FlowCycle principles, operations have the potential to achieve:
- A 20–30% uplift in underground development performance using the same fleet;
- A 25–30% reduction in cost per metre developed; and
- A longer-term transformation roadmap that unlocks 40-50% total performance uplift by aligning operations, technology and culture.
These gains do not rely on significant capital outlay or large workforce expansion, according to MasterMined, coming, instead, from working the system differently.
By integrating those Lean flow principles, real-time constraint management and calibrated simulation, FlowCycle provides a unifying performance framework that can be scaled across operations and geographies, according to the company.
Sprague concluded: “We believe FlowCycle can do for mining what the Toyota Production System did for manufacturing – standardise excellence, unlock flow and elevate performance across the board.”