24/7 GUARDIAN FOR YOUR SCREEN
Metso’s equipment monitoring system, Metrics, connects crushers and screens giving customers 24/7 access to live data to stay ahead of the curve and make data-driven decisions in real time. It is an efficient tool to maximise uptime, optimise performance, support maintenance planning and reduce unplanned downtime. The higher performance, higher yield and tracking of future process monitoring enables significant sustainability improvements for a greener future. Metso’s Metrics leaves no stone unturned!
Screening out issues with remote monitoring
Think of Metrics for screen monitoring as a 24/7 guardian for the screen: it’s an integral part of reducing unplanned downtime and extending its lifespan. More importantly, it optimises screen performance to help perfect your overall process. It is, however, important to remember that Metrics is not limited to screens but can also help companies monitor their entire plant. There are also retrofit kits with the sensors available to install on older Metso screens, as well as on screens from other suppliers.
Having the main customer challenges and aims in focus, Metrics offers many benefits that are sought after by the mining industry.
Possibility to avoid potential breakdowns
Intelligent monitoring is all about optimising performance and preventing issues that cause downtime. Metrics monitoring enables operators, controllers and service professionals to see real-time analysis of vibrating screen performance and bearing condition. If there is a problem, the system sends an alert, offering a chance to perform necessary maintenance before a minor issue becomes a major expense.
Clear overview of operation – easy and fast
Metrics monitoring is designed for intuitive operation. An easy-to-read screen dashboard with OEM insights makes it possible to detect issues well in time. The integrated system delivers complete diagnostics, alarms and history at a glance. Modular sensors are wireless, self-powered and easy to use. All components are engineered to be reliable, even in the toughest mining environments.
Maintenance planning ahead
Knowledge about improper motion caused by events such as broken springs, insufficient structural support and/or incorrect run speed, etc offers a chance to plan maintenance breaks, keeping the downtime as short as possible and avoiding unnecessary safety risks.
Optimise the process in a sustainable way
By collecting data in real time, it is possible to get access to fault-finding recommendations and be able to quickly analyse trends. This makes it easy to try different parameter settings in order to optimise the process according to the current conditions and targets. It will also have a positive effect on sustainability as running the screen in an optimal way enables increased uptime and less consumption of eg media and spare parts. Using fewer parts translates to less waste ending up in landfill.
Getting the most out of your production
Metrics for screens monitoring system has proven its value with Metso customers globally. One customer in Finland highlighted three cases where potentially costly breakdowns were avoided because of remote monitoring with Metrics:
1. Exciter temperatures exceeding the limits
Through remote monitoring, Metso noticed that the MF series screen’s left exciter temperature showed 75°C, which was clearly higher than usual. There was also an increase in bearing noise in the trend view. The customer was informed and was asked to check with a thermographic camera and to also check the oil. With the temperature increase confirmed and particles and dirt found in the oil, the customer started planning for an extra stop three days later. The early warning gave them time to fill intermediate storages of ore so that they could change out the exciter without losing production. The old mechanism was sent for maintenance and will be returned to the site for use as a spare.
The likely consequence if not detected early could have been a total breakdown with major damage to the screen structure. A breakdown would have caused a maintenance stop of at least eight hours and a bigger safety risk.
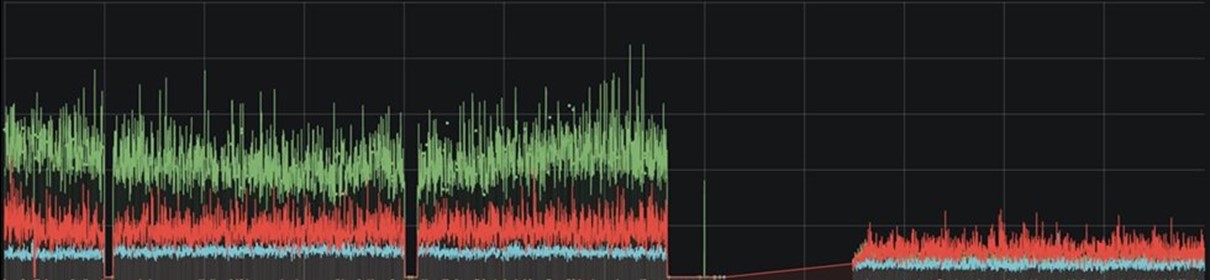
2. Missing sideliners
A potential failure in the RF series screen was detected. A clear difference in orbits, motion acceleration and especially feed left transverse acceleration and motion were noticed via the monitoring system. The customer was informed right away and made the decision to stop the screen the day after to check. The finding was that two sideliners were missing – most likely they had somehow become loose and dropped. New sideliners were installed and the normal screen operation was restored.
If the missing liners were not detected, the consequences would have been excessive wear of the screen body, but more than that, a typical subsequent failure could result in serious damage to the screen deck frame caused by the flapping screen panels. In addition, with liners coming loose, panels may dislodge and have the potential to cause major issues downstream.
3. Rock blockage below the isolation frame
The system showed a deviation in how the MF series screen was operating. The orbit’s shape was different at the discharge end. When the customer checked the screen, they discovered that a rock was blocking the isolation frame. The rock was removed, and the screen was put back into operation. The blockage did not cause any damage to the screen body.
If not detected early, one consequence could have been structural damage to the isolation frame or the screen body, not only due to the physical contact but also due to the uneven motion over time.
Read full customer case on the Metso website: Avoiding major breakdowns with the help of monitoring – Metso.
Optimising the screening process
Jan Wirth, Director of Screening Technology at Metso, is heavily involved in Metrics for screens. “Ultimately, the goal is to identify problems early, which then gives the operator time to react, to plan or prepare, and to increase the availability of the equipment,” Wirth says. “It allows us to work closely with our customers to support their digitalisation journey and any operational challenges along the way. At the same time, they can increase sustainability by optimising performance and reducing downtime.”
So far Metrics for screens has brought significant improvements to multiple customers’ screening operations. “One of our mining customers with a 24/7 operation has increased uptime and availability by 1% based on acting early to prevent problems,” Wirth says. “Miners want to be sure their equipment is up to par since they are aware that every minute the equipment is not running results in lost production and profits.
“To give some rough numbers, we say that a customer who detects a maintenance issue early on with Metrics before experiencing unplanned downtime will improve uptime. We estimated the reduced downtime based on detected events over a year and calculated this to be 1% as availability gain in their 24/7 operation with 95% availability target.”
The Metso Metrics monitoring system for screens is an efficient tool to maximise uptime. It helps you optimise the screen performance, supports maintenance planning and reduces unplanned downtime. Everything you can plan for will save costs and reduce expensive downtime.