ABB: Pioneering Gearless Mill Drive Technology
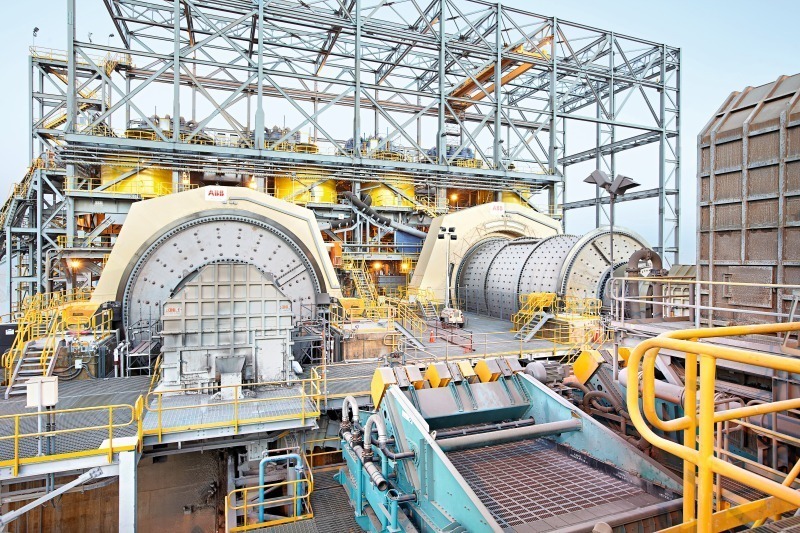
ABB has always been the front runner in Gearless Mill Drive (GMD) technology, a unique mill drive concept, eliminating all mechanical transmission parts by mounting the rotor poles directly onto the mill shell and wrapping the stator around it; basically, the mill itself becomes the rotor of the motor. The GMD provides the highest possible mill power rating combined with the inherent variable speed capability, which opens the door to a variety of operational flexible options to maintain energy-efficient grinding during fluctuating feed conditions.
ABB (Brown, Boveri & Cie at that time, before the merger with Asea) started its GMD story in 1969 with the commissioning of the world’s first GMD (6.4 MW) for a 16-ft (4.9 m) diameter cement mill in France. Some 6.4 MW of installed power was, in the sixties of the last century, too much power for geared mill drives and, therefore, ABB realised the truly visionary idea of the GMD. It’s noteworthy that this first GMD is, more than 50 years later, still in operation, proving the robustness of the concept. Afterward, numerous other cement mills were equipped with GMDs and, in the eighties of the last century, the GMD entered the mineral processing industry.
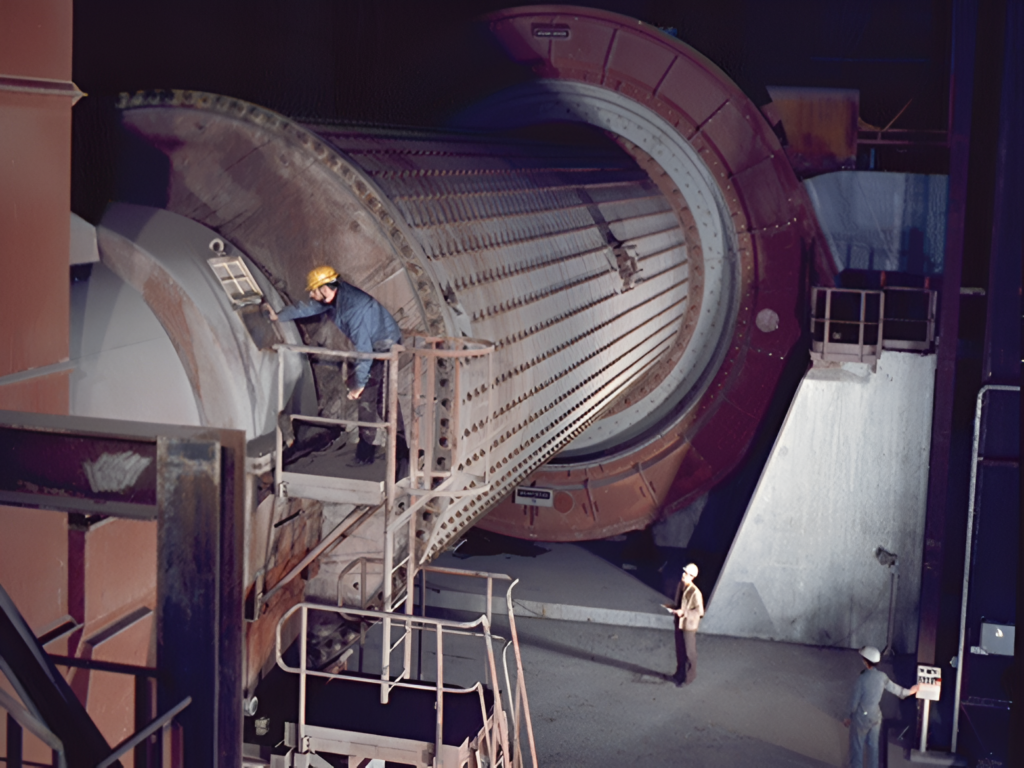
Over the last five decades, larger orebodies with increasingly low grades have led to advances in mill technology and larger diameter mills – all corresponding to higher installed power ratings. About 15 years ago, ABB was the first company to manufacture GMDs for the world’s most powerful SAG and ball mills: a 28 MW GMD for a 40 ft SAG mill and a 22 MW GMD for a 28 ft ball mill. Later, another 28 MW GMD for the world’s first and only 42 ft SAG mill. Today, ABB has sold twenty GMDs for 40 ft SAG mills, some of which have already been running for more than a decade. ABB was also the first supplier to supply a 22 MW GMD for a 28 ft ball mill, and, today, twenty GMDs of this size have been sold. The story continues, as the main mill suppliers and ABB are working together on even larger mills: 44 ft SAG mills and 32 ft ball mills with around 34 MW.
For the transport from the Ring Motor factory in Bilbao, Spain, to the site, the stator of the GMD motor is typically split in four parts; for the smaller balls sometimes into only three parts. However, ABB was the first and only GMD supplier to ever split the GMD stator into more than four parts, which was required by project-specific transport restrictions (dimensions and/or weight). This was required for a 25 ft ball mill in Chile and for a 40 ft SAG mill in Canada. To supply the stator in more than four parts is not a trivial task, as each additional split is reducing the stiffness of the stator. However, ABB’s typical GMD stator design is characterised by a high stiffness value, and with certain additional measures the additional split was indeed technical feasible.
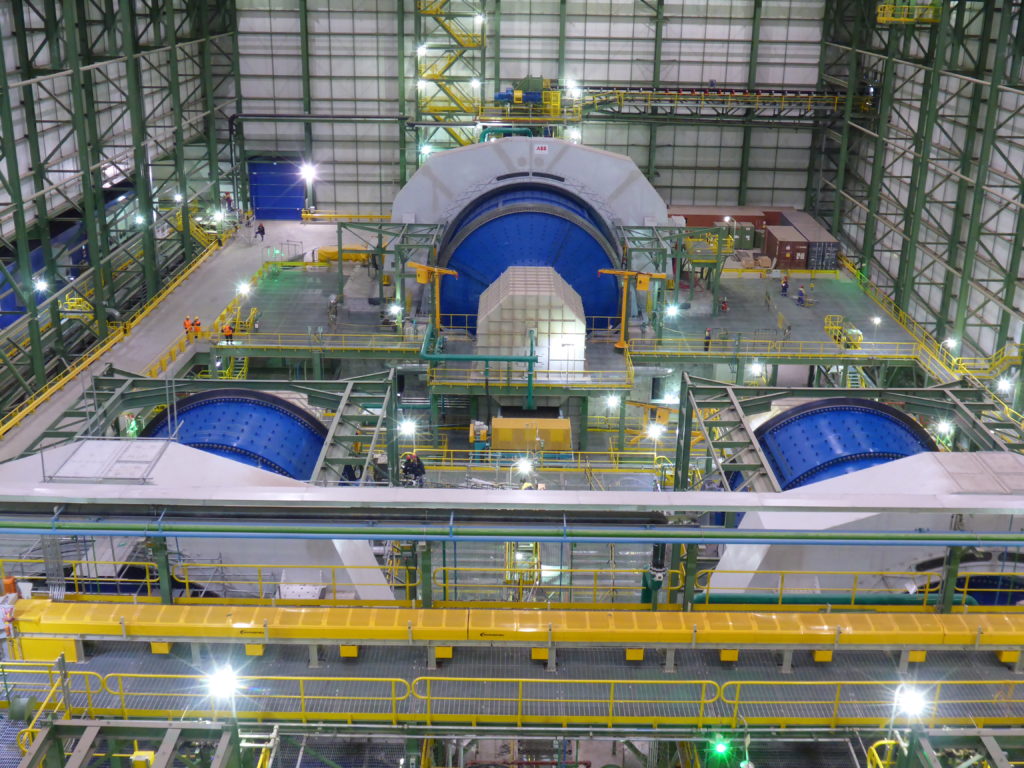
ABB has sold by far the largest total amount of GMDs, currently 154 units and counting. In 2006, ABB started in Santiago de Chile with its well-respected GMD User Meeting, which is a great networking platform for stakeholders in the GMD community. The GMD User Meeting is not a sales and marketing event, but a podium where operation and maintenance engineers from sites with ABB GMDs can exchange experiences. Typically, around half of the presentations are from non-ABB engineers, and the fascinating discussions at the GMD User Meeting are also a potential source of ideas for new features. Our latest gathering took place at the end of August 2023.
When it comes to new installations, if mill availability and efficiency are truly of paramount importance, then the GMD comes automatically into the spotlight: availabilities higher than 99%, including regular GMD maintenance, and drive efficiencies of over 95% are achieved. This is accomplished primarily because the GMD has eliminated – as much as possible – all mechanical components such as ring-gear, pinion, gearbox, coupling or air-clutch, motor shaft and motor bearings: what is not there cannot fail or cause efficiency losses.
Energy efficiency on mill drives is pivotal as they are by far the largest power consumers not only in the plant but even in the region, and therefore energy-efficient GMDs really matter (as has also been acknowledged in ABB’s recent Sustainability Report 2023 – see page 23). Furthermore, the high availability is possible because the GMD is comprehensively monitored. More than 15 years ago, ABB pioneered GMD remote monitoring. Another impressive milestone was the paper ‘ABB Ability™ – Digitalization of Predictive Maintenance for Grinding’ (SAG Conference 2019, Vancouver), presenting the concept of automatically pushing GMD signals into the cloud instead of arduously logging in remotely. At the following SAG conference last year, ABB demonstrated further progress with the paper, ‘Remote Mill Monitorization: A Solution for Higher Efficiency and Asset Optimization.’
Today, sophisticated algorithms analyse the enormous amount of data generated continuously by the large installed fleet of ABB GMDs, looking for unusual trends that could provide early warnings of possible anomalies. As Zurich Insurances and ABB described in their joint paper ‘Insurability of large gearless mill drives’ (SAG Conference 2011, Vancouver), the target is to prevent any unscheduled mill shutdown.
ABB is now bringing its GMD Transient Recorder to the next level. In the exceptional event of a GMD trip, the high-resolution Transient Recorder records a large, predefined set of signals in a short time window from several seconds before until a few seconds after the trip. This information provides tremendous assistance in troubleshooting to find the root cause and, if necessary, take countermeasures to prevent similar trips. However, while the pressure is high due to the unscheduled mill shutdown, the end-user engineer either needed to download the large Transient Recorder dataset and send it to ABB for analysis, or the ABB engineer logs in remotely to access the data. In both cases this may result in additional delay before starting the actual troubleshooting: the GMD rarely trips and, therefore, the end-user engineer typically does not have experience in downloading the Transient Recorder data, while on the other hand it may be challenging to establish the direct remote access due to on-site IT restrictions and modifications. ABB, therefore, developed the next level Transient Recorder, which in case of a trip pushes the data automatically into the cloud and the ABB engineer (or an end user’s GMD expert) can access it conveniently from anywhere in the world and start troubleshooting immediately.
