Investigating the sustainability benefits of using mine hoists, and how to increase the efficiency of existing installations
Hoists are key to enabling sustainable underground mining, especially as mines go deeper. Importantly, the technology has been available for decades and can be powered by green energy.
“We’ve been working with developing world-leading mine hoist solutions for over 130 years. A mine hoist system is very much a low-carbon alternative for vertical ore haulage as well as a proven solution for underground mines,” explains Björn Jonsson, Global Business Line Manager, Hoisting at ABB. “Powered by electricity with the possibility to run off renewable energy sources, hoists are also able to run autonomously with high efficiency and impressive operational life.”
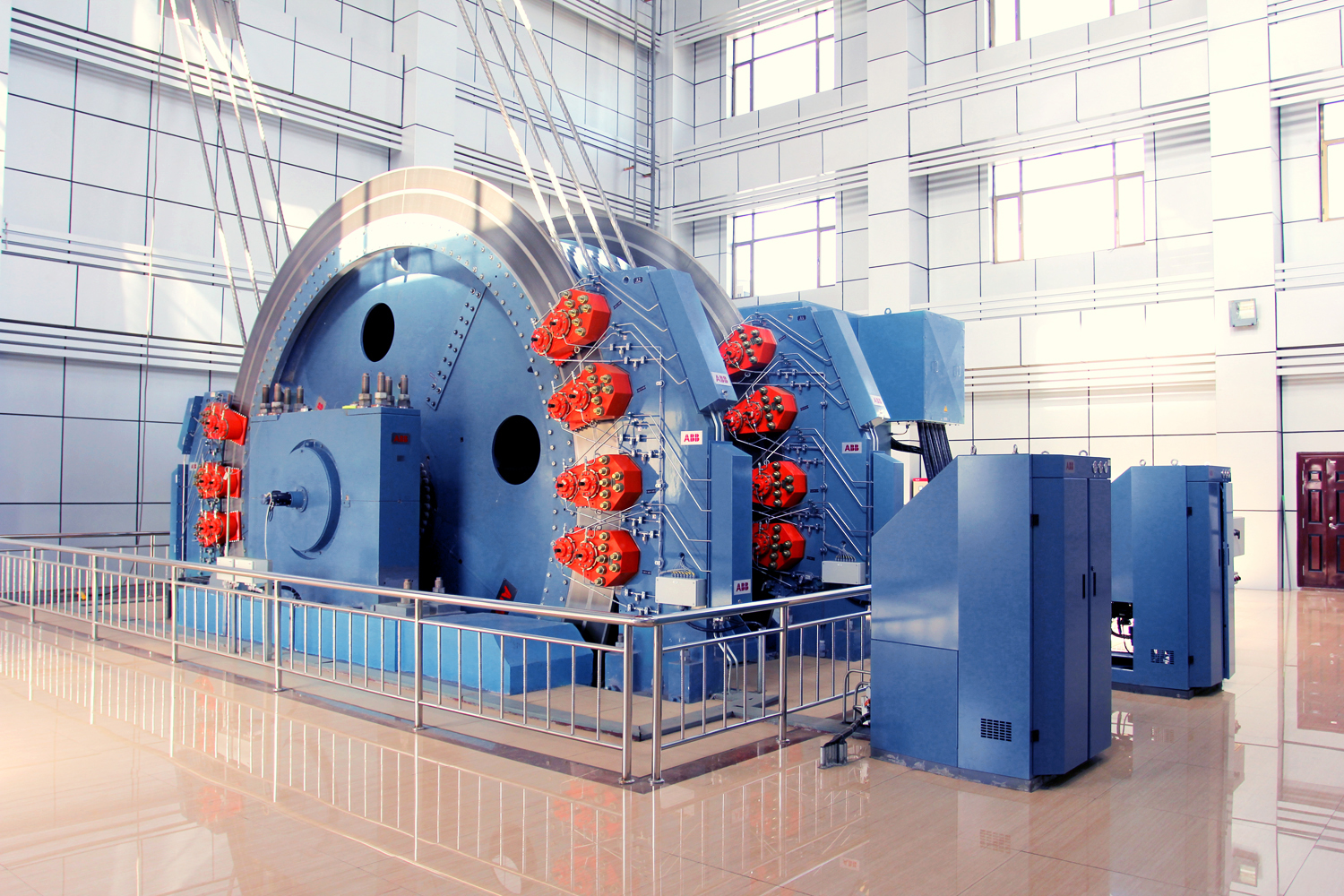
Ore haulage is one of the most energy-intensive activities in a mining operation, and while a mine hoist in many cases is the most energy-efficient alternative, also offering low environmental impact, there are still several factors that needs to be considered from a sustainability aspect. In a lifecycle analysis issued by ABB, it was concluded that the largest environmental hotspot in a mine hoist system is the electricity consumption, followed by material use in primarily ropes and skid plates. In fact, depending on the electricity mix, it is possible to save up to 266,000 t of CO2e (according to a report from Chalmers University). If we divide that number of 266,000 t CO2 saved over 25 years, it equals the yearly emissions of almost 2,500 gasoline-powered passenger vehicles, or the yearly energy usage of about 1,300 homes.
Additionally, circular initiatives such as using materials in a more effective way and extending their lifetime could also offer significant environmental savings.
This makes the selection and design of the hoist system a crucial part. For a long time, ABB have been leaders in creating energy efficient drivetrain solutions, offering remote health and monitoring services to ensure the highest possible efficiency. Looking at the energy consumption for each hoist cycle and analysing how peak energy is optimised within the entire mining operations is another important factor. For example, large energy efficiency wins can be found when exploring alternatives for heat recovery, recycling the heated air from the motor and chiller. For instance, the recovered heat could be used to heating the hoist room or even heating the shaft air ventilation when the ambient temperature is low. Applying this type of circular approach is key to reducing the overall environmental footprint while simultaneously increasing the efficiency of the entire mine hoist system.
“While we already know that mine hoists offer an overall low environmental impact, we should always strive to do better and help our customers reduce their environmental footprint,” Jonsson says. “Our capability of delivering the entire mine hoist scope enables us to have a significant impact on how the hoist systems are constructed, both when it comes to material use but also accounting for the overall supply chain.”
To read the entire ‘A zero-emissions, sustainable mining solution’ whitepaper,