Energy innovation in action: Metso pilots PROSCON® Energy Management System
As energy efficiency became a key priority within the mining and metallurgical industry worldwide, operations are increasingly adopting advanced Energy Management Systems (EMS) to optimise production, reduce costs and support sustainability goals.
Metso has begun the process of productising and integrating EMS to Metso PROSCON®. This development is taking a significant step forward by implementing the PROSCON EMS as a pilot project at the Direct Reduced Iron (DRI) Smelting Furnace in Pori, Finland. This initiative further highlights Metso’s commitment to innovation and sustainability.
The rising demand for energy management
Energy management has become a critical concern for businesses due to both environmental and economic factors. Global climate initiatives, rising natural resource costs, company-specific sustainability goals and stringent government regulations have pushed companies to adopt structured approaches to managing energy consumption. Carbon dioxide emissions and energy use are among the top impacts on automation, real-time monitoring and data collection.
Beyond important regulatory compliance, companies also recognise the fact that energy costs significantly impact competitiveness and profitability. Since modern business operations rely heavily on energy to operate, the direct impact of energy price fluctuation is quite significant. By implementing an effective energy management system, operations can not only reduce expenses but also demonstrate their commitment to corporate social responsibility – all at the same time.
Introducing: Metso’s PROSCON Energy Management System
To address these challenges, Metso is introducing the PROSCON EMS – an energy management system designed to enhance operational efficiency through continuous monitoring and data-driven decision making. The system provides real-time insights into energy consumption patterns, helping operations optimise their energy use whilst ensuring compliance with evolving regulations.
“If we can’t measure things, we can’t control things,” says Mikko Pulli, Product Manager, Metso PROSCON Process Control System. “We’ve been developing the PROSCON EMS as part of the process electrification so that we can provide a tool alongside the process electrification to our customers. We collect all the energy consumption data from the process and provide reports based on real data, and this allows customers to continuously develop.”
With predictive analytics and proactive maintenance, PROSCON EMS also integrates seamlessly with Metso’s metallurgical digital twin technology, Geminex. By combining systems, sites can reduce operational costs, minimise environmental impact and gain a competitive edge in an energy-intensive industry.
“Customers will be able to understand all energy consumption data and make better, knowledge-based decisions. Electrical energy information is natively associated with the electrical distribution and motor control systems, which are connected to process control,” says Veli-Matti Järvinen, VP, Automation at Metso. “System enables energy management reporting and an online system where operators and production management can analyse the energy data, create improvement initiatives and track their effectiveness – all without compromising safety, production or quality.”
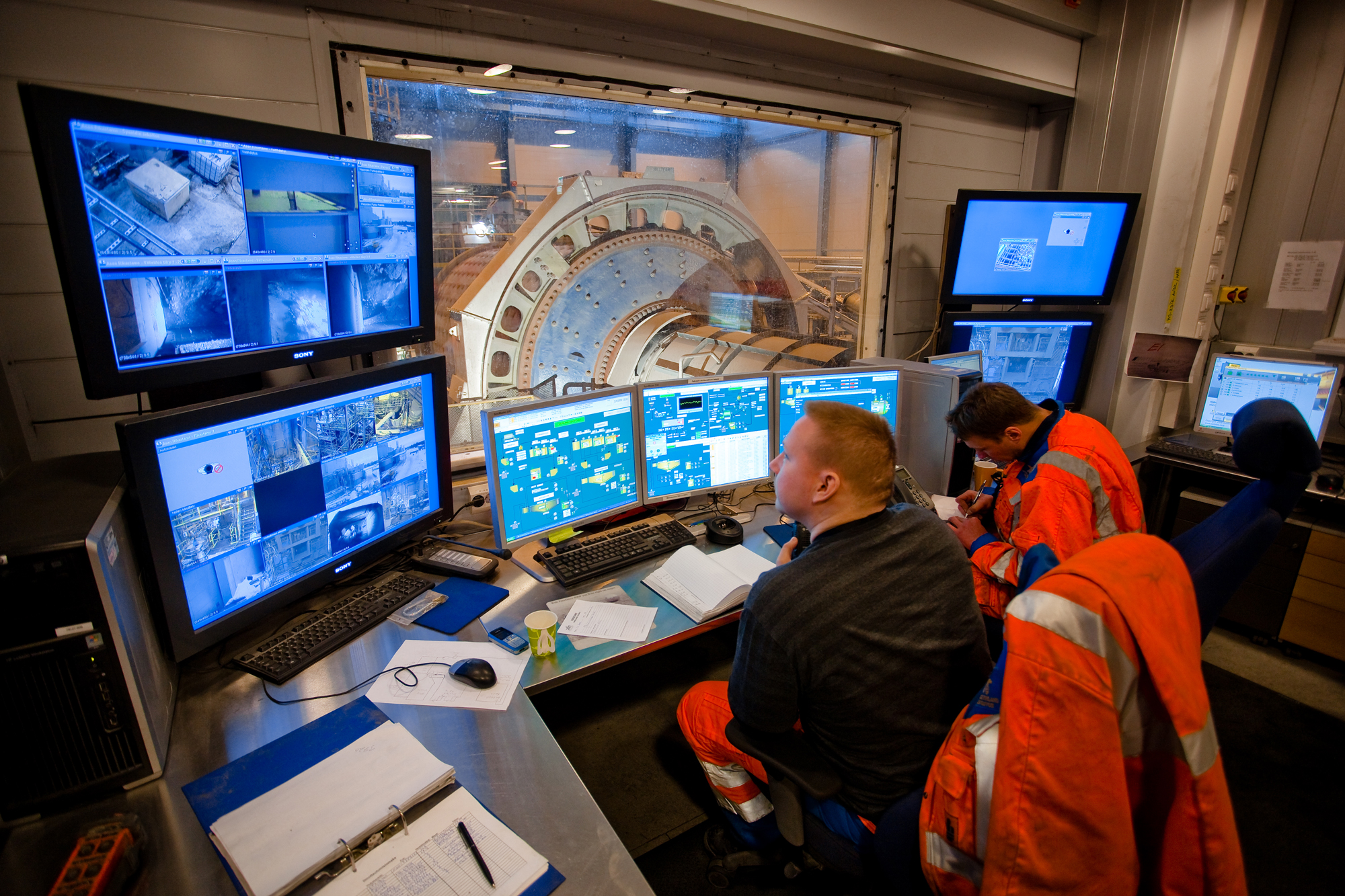
Beyond compliance: The key benefits of energy management
According to the ISO 50001 framework, a structured energy management system can lead to many advantages, including systematic energy use reductions, improved environmental performance and, of course, enhanced operational efficiency.
“Customers need to understand the process, and that’s only possible when they can measure it,” says Järvinen. “Once they measure and understand the details – such as the relationship between energy use and changes in process conditions – they can control and optimise operations. It’s this continuous improvement that drives development forward.”
Key advantages of Metso’s PROSCON Energy Management System include:
• Maximised efficiency, minimised costs: The system enables continuous monitoring and optimisation of energy performance, improving asset utilisation and reducing maintenance costs.
• Regulatory compliance: PROSCON EMS ensures compliance with current regulations and can quickly adapt to future regulatory changes, minimising business risks associated with energy use.
• Reduced carbon footprint: By improving energy efficiency and aligning with other sustainability goals, PROSCON EMS helps operations lower their environmental impact.
• Data-driven decision making: The system integrates intelligent energy and power devices with advanced software for comprehensive data collection, visualisation and reporting.
• Future planning: This is where power management goes beyond mere measurement. With digitalisation software and smart analytics, operations can follow up their KPIs and ensure future success.
“With Geminex planning and scenario analyses, the integration also enables full-plant energy consumption simulations and more accurate process models,” says Järvinen. “This allows us to anticipate when and why the plant might require more energy, which is critical in regions with limited energy availability or reliance on locally generated power.”
Having access to accurate energy consumption data is also essential for data-driven decision making. For example, while plant managers may know the total energy consumption of their facility, they may lack visibility into the energy usage of specific equipment. With PROSCON EMS, overall energy consumption – such as that of a concentrator plant – can be measured and analysed.
In addition, when the entire process electrification is equipped with detailed measurement capabilities, energy usage can be further broken down by specific areas, such as comminution, separation, filtration or thickening. Or, more specifically, individual equipment such as large pumps can be monitored to identify opportunities for efficiency improvements. This level of insight not only empowers operations to optimise processes but also drives sustainable energy use – an important topic at the forefront of today’s industry landscape.
“Energy management systems should be implemented when renewing or building new plants where process automation and electrical distribution systems are already being developed,” says Järvinen. “The additional cost of integrating PROSCON EMS is minimal or even completely negligible in some cases, so it’s important to encourage customers to consider these opportunities.”
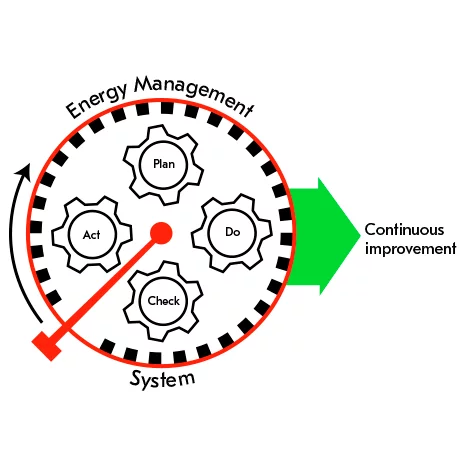
Aligning with ISO 50001 standards
ISO 50001 is an internationally recognised standard providing organisations with a structured approach to improving energy performance. It follows the Plan-Do-Check-Act (PDCA) methodology, ensuring continuous improvement in energy management.
“PROSCON EMS enables customers to practice a continuous improvement cycle in energy management,” says Järvinen. “If they choose, it also supports ISO 50001 certification since the system meets the necessary technical requirements.”
By aligning with ISO 50001, PROSCON EMS helps companies establish clear energy policies, conduct energy audits and set measurable performance targets. This enhances energy efficiency strategies and supports long-term sustainability initiatives.
“Sustainability is possibly the most important factor in a company’s social license to operate,” says Järvinen. “CO2 emissions reporting is a key KPI, and reporting must be standardised or even approved by local officials. The data must be trustworthy, and this system ensures data accuracy and reliability.”
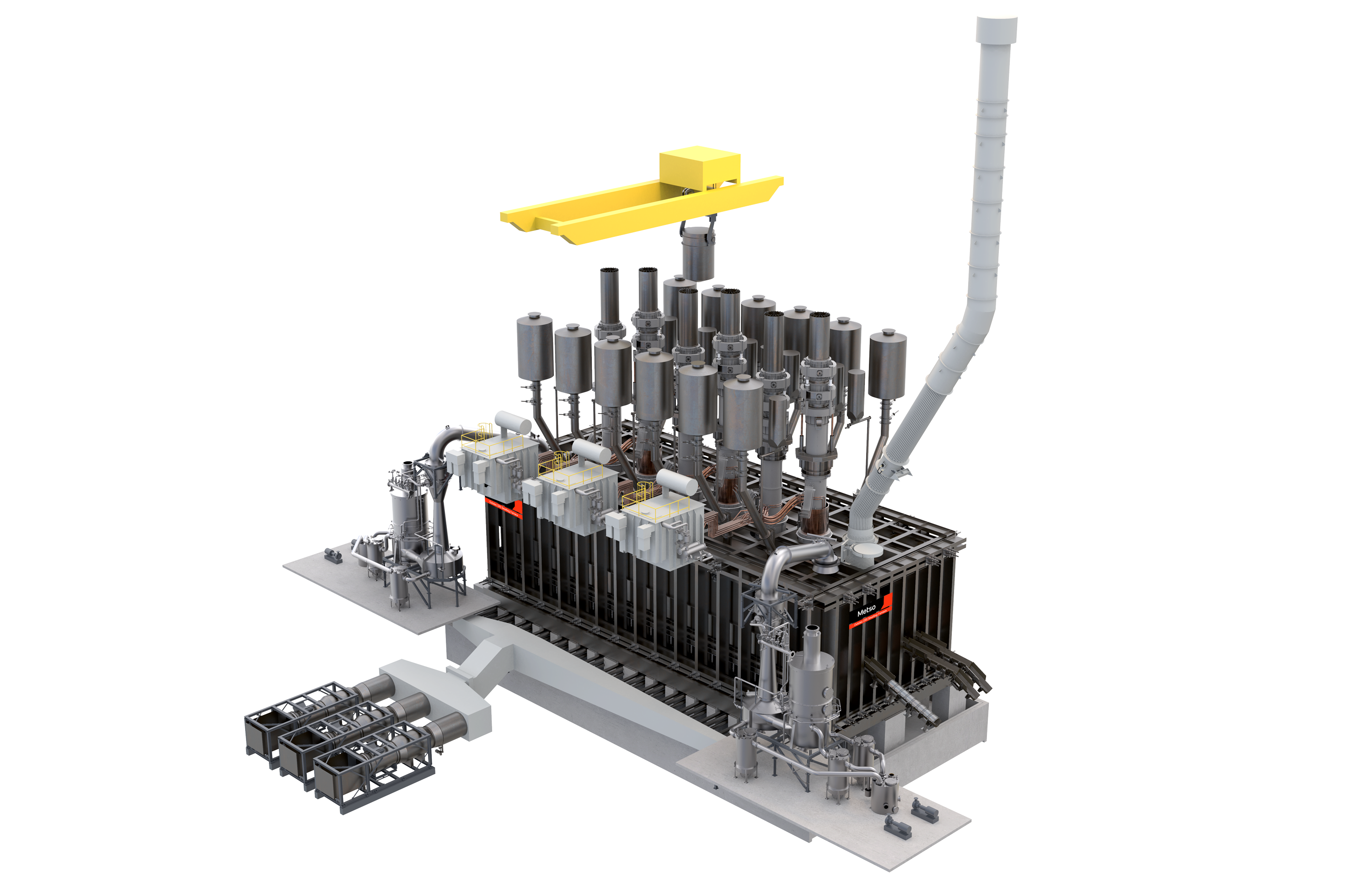
Testing PROSCON EMS at the DRI Furnace in Pori
Metso has recently expanded its pilot capabilities at the Metso Research Centre in Pori, Finland. Among the latest projects is the DRI Smelting Furnace pilot facility, which serves as a testing ground for developing metallurgical processes. Now, Metso is planning to use the facility for the PROSCON EMS.
“We chose the Pori DRI Smelting Furnace as the pilot site because this compact installation integrates both medium- and low-voltage distribution systems, along with variable speed drives. It includes power quality measurements and busbar temperature monitoring for the medium-voltage distribution system. This setup allows for seamless connectivity verification, efficient system setup, and detailed reporting on various functions,” says Pulli. “The bonus is that after installation and commissioning, the research group can collect additional energy usage data, such as kilowatt consumption per ton of raw material or something else specific, so we will have that extra data.”
The installation of PROSCON EMS at the DRI Furnace aims to collect data, improve transparency of energy consumption and validate the system’s capabilities in real-world applications. The commissioning of the pilot system is planned for the first half of 2025 and will mark a significant milestone in Metso’s journey toward intelligent energy management and sustainable industrial operations.
“Here at Pori, we have excellent facilities and strong collaboration across business areas,” says Jukka Köykkä, Maintenance Manager at Pori.
From pilot to progress
“The cost of energy is rising, especially in Europe, but it’s also related to the social license to operate.” says Pulli. “Large plants consuming vast amounts of energy impact overall energy consumption in surrounding areas. If we can optimise that, it benefits both the operation and the community.”
As industries worldwide prioritise energy efficiency, Metso’s pilot project serves as a benchmark for integrating cutting-edge energy management solutions within mining and metallurgical processes. By aligning with ISO 50001 principles, the system provides a structured and data-driven approach to optimising energy use. That’s why, together, we are the partner for positive change.