Hiding in plain sight – practical ways to make sustainability gains
With mounting pressure on mine operators to reduce their environmental impact, many sites are re-examining their circuits to find improvement opportunities as they push to achieve net-zero status. There are several focus areas that tend to receive the most attention, such as looking for efficiency gains in energy-intense grinding operations or searching for ways to save on water consumption across dewatering process stages.
However, there is one overlooked area that is often hiding in plain sight. At every stage of the mineral processing circuit, equipment and components are subject to high rates of wear and tear, resulting in tonnes of metal, rubber and other worn machines and parts sent to landfills. Replacing equipment and components also involves high levels of carbon emissions from the manufacturing process coupled with fuel costs from transport. It is worth exploring ways to extend the lifespan of assets, which can have a tremendous impact over time.
Crushers, conveyors and mills are integral to mining operations but are all subject to the abrasiveness of the ore. Looking for things ‘hiding in plain sight’ such as identifying practical ways to extend the lifespan of equipment and the associated wear and spare parts to reduce waste, not only contributes positively to the environment but also to your bottom line.
The use of durable materials and cutting-edge technologies can ensure that parts and equipment last longer and need less frequent replacement — keeping them out of landfills and reducing your maintenance costs. By enhancing performance and reliability, these wear parts and systems support a more sustainable and eco-friendly approach, all while integrating advancements into everyday use. Here are some ways to integrate these features into your operations.
Optimising wear and spare parts
Caring for your crusher with long-lasting wear parts and value-adding upgrades provides a great opportunity in protecting your equipment, reducing downtime and contributing to more sustainable operations. High-quality protective wear parts can support safeguarding your crusher and synchronising maintenance cycles. Specially engineered protectives provide added benefits. For example, Metso Poly-Cer protective wears offer up to three times the wear life and reduce the need for ‘quick-fix’ solutions – lessening material waste.
When considering a crushers working wears, maximum life solutions such as MX for cones offers up to double the wear life. Deeper optimisation services of wear parts help you develop your crushing process and identify improvements, such as through chamber alloy selection and customisation of profiles. Optimising the crusher chamber can contribute to higher production rates, crushing efficiency and reduced downtime.
Upgrades can also contribute to a longer lifespan for crushing equipment. The Metso Xtreme forged head, for example, offers unparalleled durability and resilience. Created from a single forged block of steel, this head is engineered to withstand the most demanding crushing applications, lasting up to three times longer than standard cast heads.
This enhanced durability means fewer replacements and less frequent maintenance, which not only reduces operational downtime but also minimises the need for spare parts. Consequently, this leads to a reduction in waste generated from mining operations, aligning with sustainability goals. By maximising productivity and minimising waste, the Xtreme forged head provides a robust solution for efficient and more eco-friendly crushing operations.
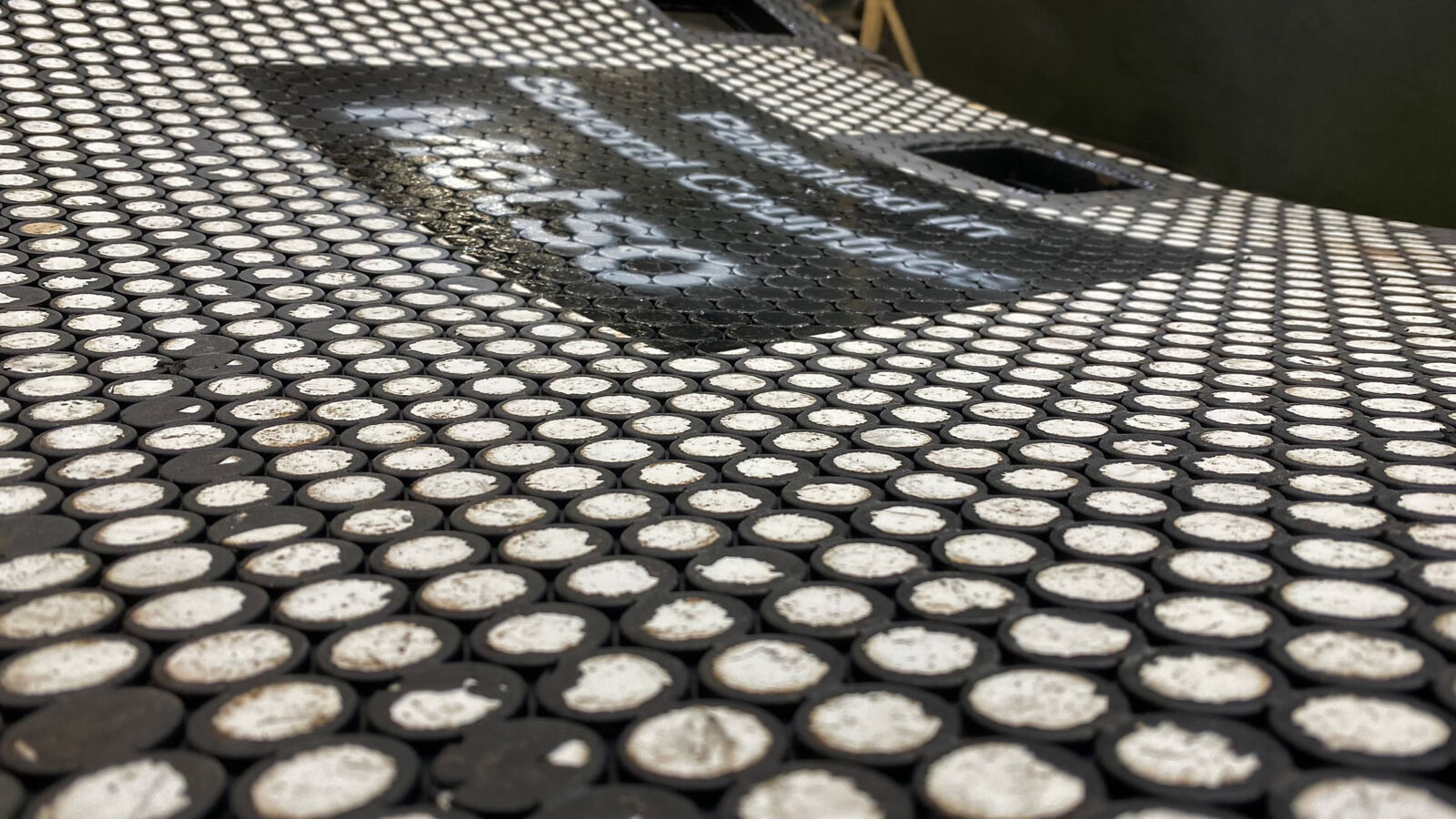
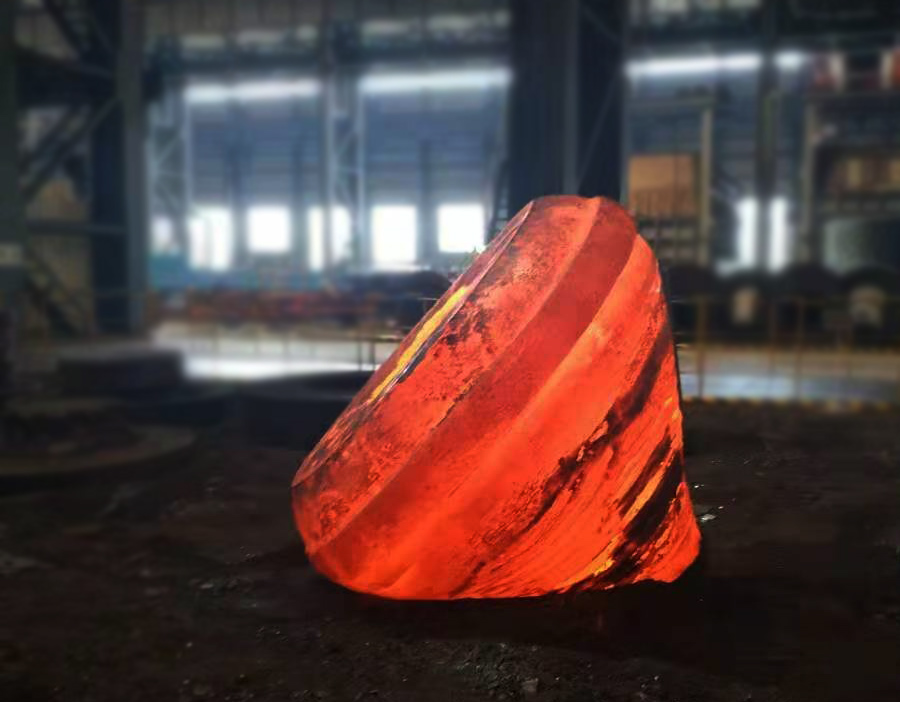
Conveying savings
Conveyor systems are another piece of equipment that needs to endure the wear and tear of abrasive material flows. Multiple parts need to be replaced regularly such as idlers, rollers and most importantly the belts themselves as they experience wear. For conveyor systems, ore falls directly onto the belt in the impact zone, and over time can result in significant damage. To get more life out of the conveyor belt, protecting it in the impact zone with an impact absorbing upgrade can make a big difference.
Conveyor impact bars and cradles offer you significant benefits for both cost savings and environmental sustainability. These components are designed to protect your conveyor belts from damage caused by heavy impacts during material transfer, thereby extending the lifespan of the belts and reducing the need for frequent belt replacements. This durability translates into lower maintenance costs and less downtime, which can lead to substantial savings over time.
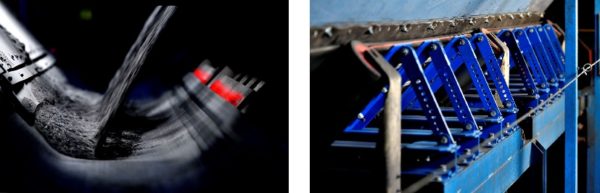
Environmentally, the extended lifespan of your conveyor belts means fewer discarded parts ending up in landfills. Additionally, impact bars and cradles help prevent material spillage and dust emissions, contributing to cleaner and safer work environments. By integrating these features into your conveyor systems, both economic efficiency and environmental responsibility are supported in your industrial operations.
Not milling around – small steps for big savings
Mill liners are crucial for the performance of grinding operations. They protect your equipment and boost production. Depending on the customers’ situation and targets, they face different challenges. Longer wear life means more uptime between stops, which is especially important when other wear parts need to match the wear life.
Metso is continuously working on developing new rubber compounds to make wear parts more sustainable and high performing. Its latest innovation, Skega™ Life rubber, part of the Metso Plus offering, extends mill liner life by up to 25%, cutting down CO2 emissions through less material use and transportation.
To get the most out of your mill liners and grinding operations, it’s also key to monitor their status. Measuring the wear helps avoid unexpected stops and lets you plan the remaining service life more accurately, predicting when replacements are needed. Inspections can also suggest improvements in material selection, optimize liner designs and pinpoint areas that need changes to balance wear life and improve grinding performance.
But sooner or later all wear parts need to be replaced. With their mill liner recycling service, Metso can separate the different liner materials, and, instead of being sent to a landfill, the different liner components can be recycled or reused in the most optimal way. By using longer-lasting and optimised liners, monitoring their status and adjusting accordingly, as well as recycling, when possible, thousands of tonnes of rubber and steel waste can be reduced over time.
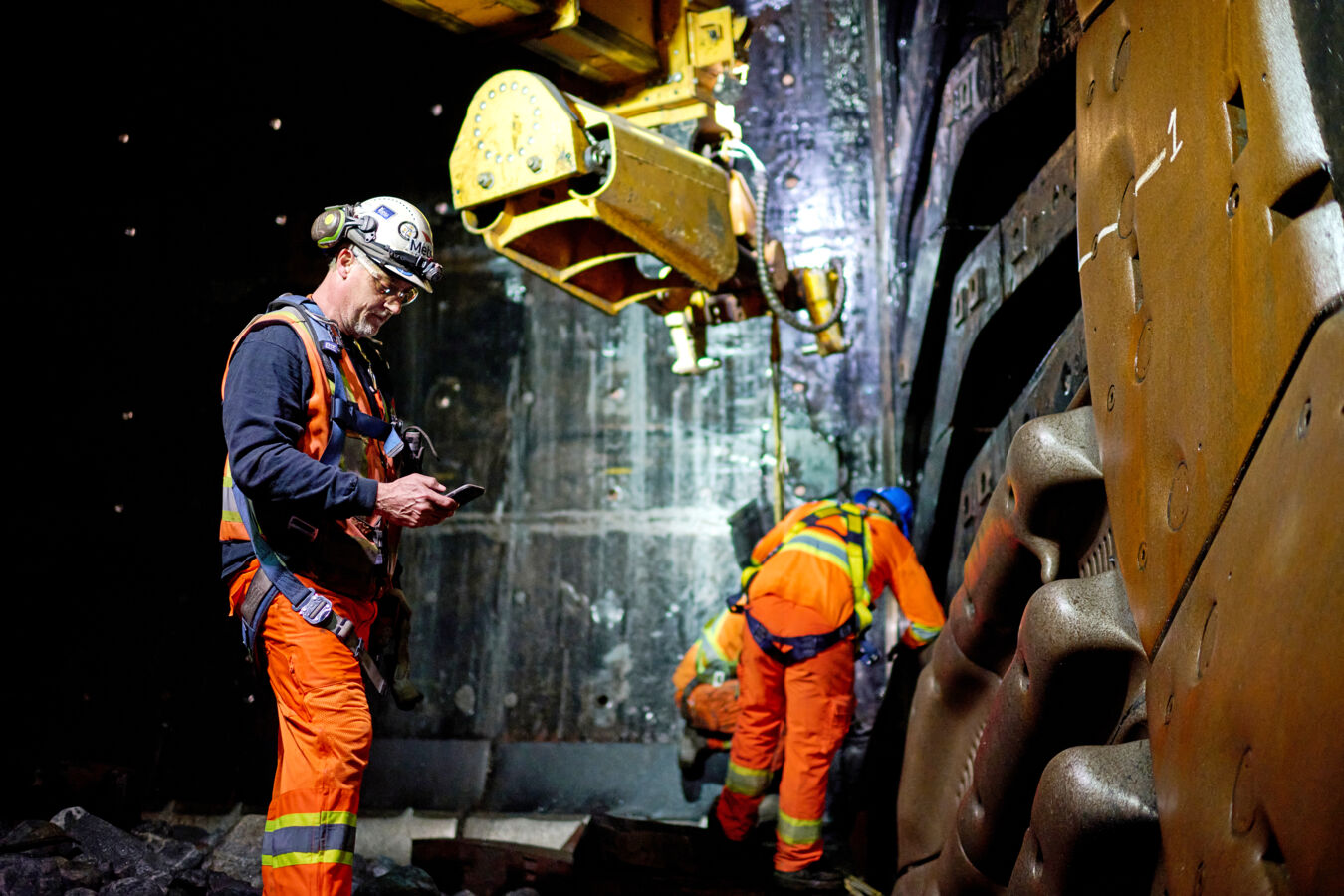
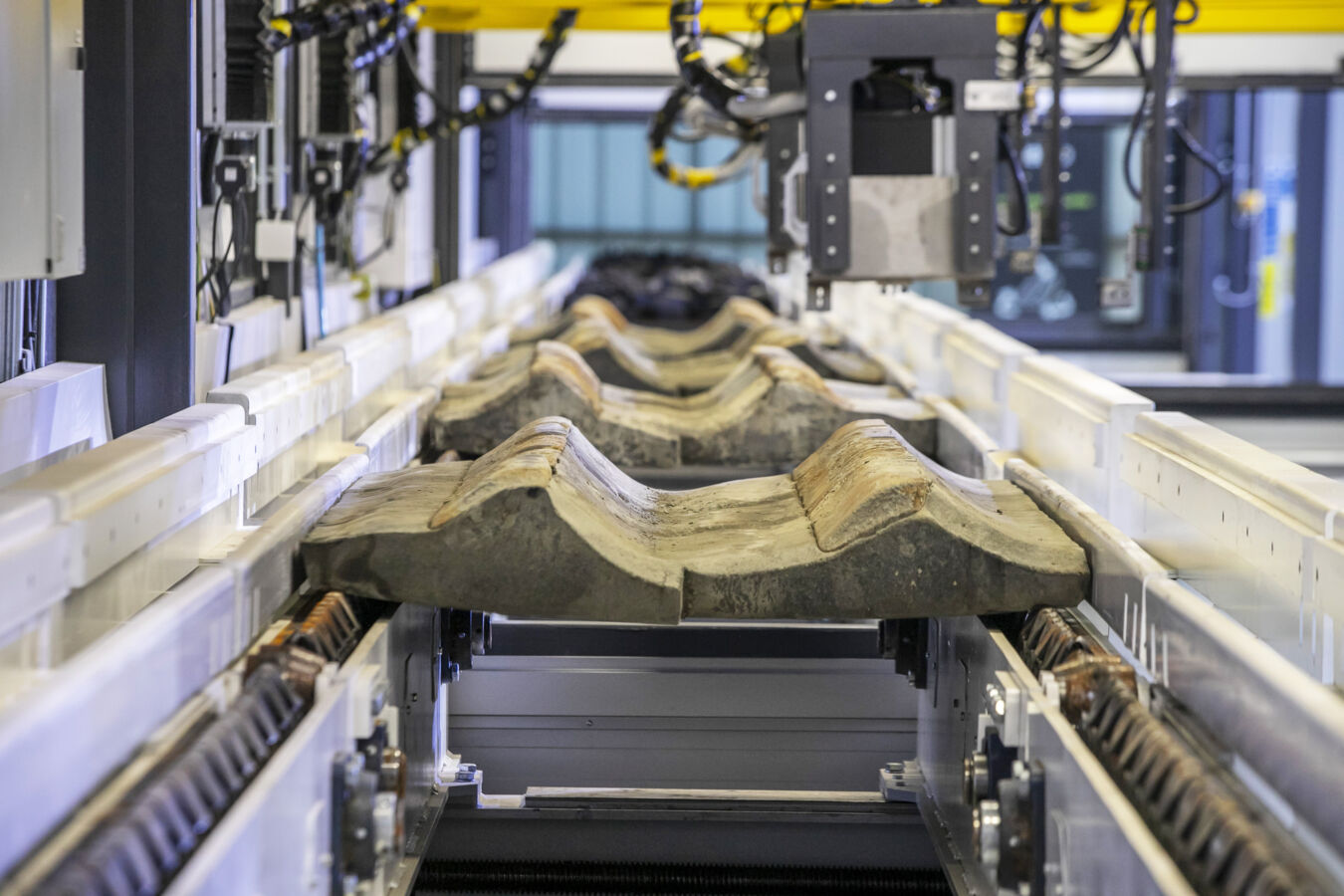
Repairs, refurbishment and upgrades – Keeping a good thing going
Once you’ve optimised your parts selection and process, even further gains can be made through ensuring diligent maintenance. Simple maintenance actions like replacing liners on schedule, regularly validating your machines components are in good working order and refurbishing worn out assemblies is a great place to start and can significantly extend equipment life. OEM refurbishment services can also play a role in restoring the original quality and performance when it comes to older equipment, ensuring maximum service life. As always, maintaining a focus on keeping your assets running for longer periods will reduce waste. Applying expert upgrades and modernisations to your older equipment can also bring you additional efficiencies as well as new features and the latest technological improvements. There is a vast range of upgrades available for crushing, grinding and conveying assets, among others, all aimed at helping your equipment and components last longer or perform more efficiently and are worth exploring.