How TireSight cuts through the noise, to help you make sense of what work needs actioning
Several years ago, as the mining industry began to shift toward autonomously driven vehicles, Kal Tire wondered: How could tyre inspections complement a more autonomous mine operation and reduce risk for technicians without too many alerts creating ‘noise’? How could we improve the frequency and quality of inspections – and the flow of critical next steps – to then enhance tyre life, safety and uptime?
Asking those questions led Kal Tire down the path of integrating autonomous inspections powered by Pitcrew AI and other sensor and IoT data into TireSight. Three years after being deployed for use on several mine sites, the company is discovering that it’s the unique layering of technology, data and collaborating expert teams that creates significant value with every passing haul truck.
On any mine site, the purpose of regular truck inspections is to ensure trucks are safe for use until the next planned service, and to address findings with least impact to availability of trucks. Traditional manual inspections, however, can present a host of challenges.
To start, technicians standing next to a 14-foot-tall (4.3-m-tall) earthmover tyre can only see about half of the tyre. With industry-wide staffing shortages hindering compliance frequency, it might be another seven days, or more, until the technician sees the other half of the tyre. When they do, their findings can vary widely: a junior inspector might believe a cut separation needed urgent attention requiring a work stoppage and repairs, though a senior inspector would know those tyres can keep running as long as it’s safe, as most cut separations are beyond repair.
Next, traditional tyre inspections see trucks brought out of service not out of necessity but because a monthly target has been set to inspect every truck each seven-day period, for example. Mining permits to operate often demand such a frequency-based approach.
“We don’t really operate in a condition-based inspection environment where inspections are prioritised, based on the conditions,” says Christian Erdelyi, Manager, Mining Technology Solutions, Kal Tire’s Mining Tire Group.
Even after tyre issues are identified during rounds of inspections, it can take days or weeks before that tyre work takes place. In the meantime, those issues could become critical. And that only covers the issues that can be seen by the naked eye.
The idea of ‘prioritising’ comes up often in talking about TireSight autonomous inspections.
“One of the big goals we had for TireSight was to ensure priority tyre work is addressed early,” says Erdelyi. With TireSight, that’s been made possible by integrating the thermal imaging camera and AI software of Pitcrew AI with Kal Tire’s Tire & Operations Management System (TOMS), to quickly identify and react to tyre-related issues that could go unnoticed.
Thermal imaging cameras are strategically placed along haul roads or near fuel bullets. As trucks pass, the cameras capture images of front and rear tyres. That footage is scanned for anomalies such as separations, hot tyres, missing tyre lugs, tread damage and more. TOMS processes the anomalies. If an issue is flagged, an off-site condition monitoring team confirms next steps. As part of a wider plan to achieve a customer’s goals for productivity or tyre life, agreed upon parameters then allow TOMS to automatically release work orders to plan and schedule tyre work like repairs and replacements. Even more, reliability analysts will look to aggregate tyre work for times when trucks are already down for other maintenance.
“Now we are on the road towards condition-based inspections, inspecting trucks according to priority,” says Erdelyi. “We’re giving time back to the team members to focus on machines that really need their expertise and reducing their exposure to trucks – but we’re still complying with the frequency of inspections set out by the customer.”
Some of Kal Tire’s TireSight customers have seen a 20% reduction in inspection downtime while automated work orders and proactive tyre work has reduced truck isolation time for hot tyre events.
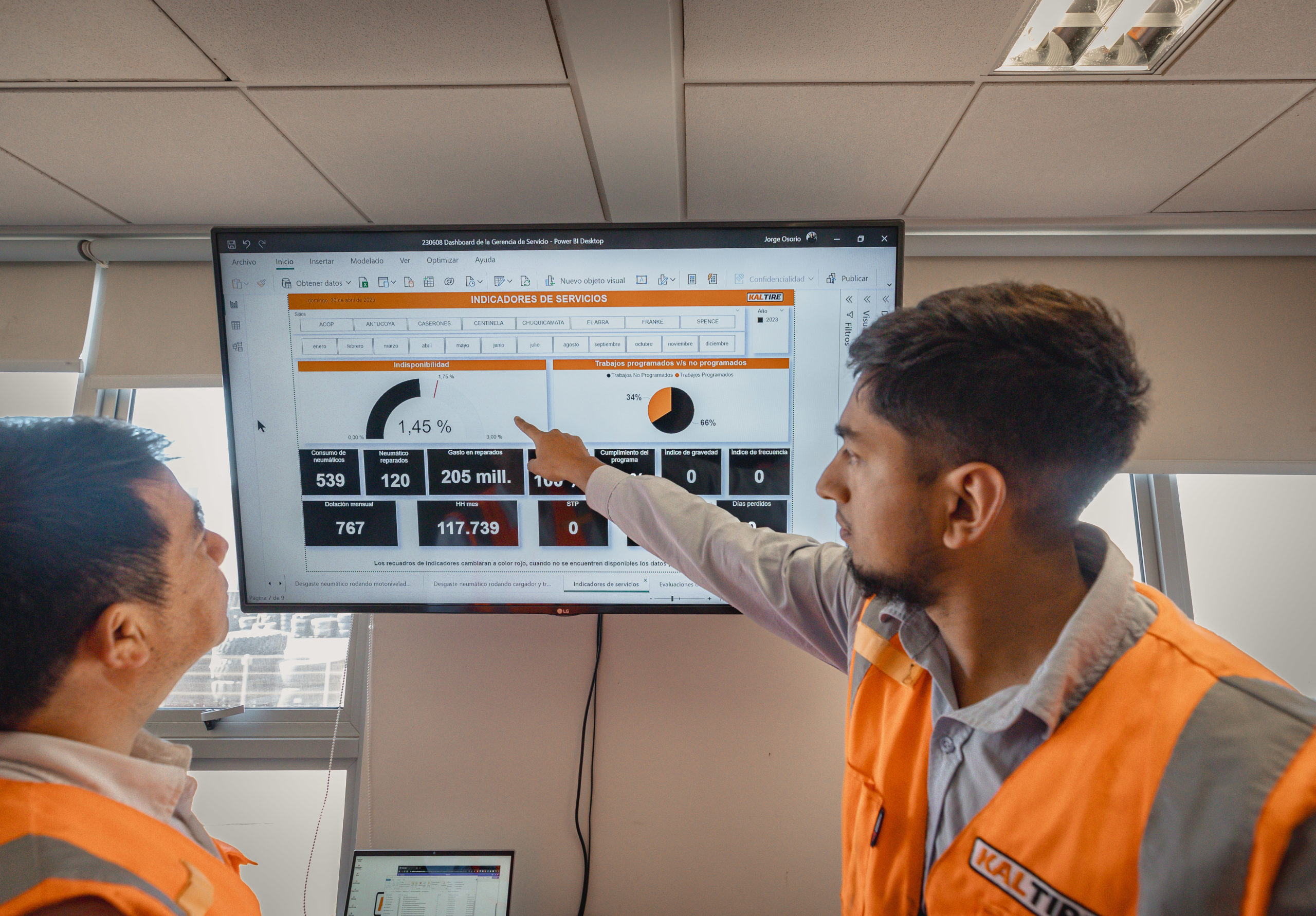
It’s the condition monitoring team that makes those results possible.
“TireSight is the fleet maintenance planning hub that ensures the work is getting done when it needs to get done,” says Erdelyi, adding TireSight integrates several data sources, including TPMS, Pitcrew AI alongside truck event and tyre performance data. “We’re summarising everything that might be happening on a mine site (in relation to tyres on trucks). We take out all the noise so the customer can see only the items that really require action.”
While TOMS plans the work to ensure operational efficiency and safety, it’s the collaboration and insights of the tyre monitoring experts that adds another essential layer to the architecture of TireSight. Kal Tire reliability analysts work with customers one-on-one at the outset to determine goals and parameters for reparable and non-reparable findings. Condition monitoring teams have been brought on board to provide 24/7 validation of TireSight anomalies. Site service teams are the on-the-ground tyre experts performing maintenance and repairs.
Now that TOMS has been in use on hundreds of sites across five continents for several years, reliability analysts are able to benchmark the data to provide influential insights about the true cost of tyre work, trending tyre performance, downtime, MTBS, haul fleet productivity and more. Three years of TireSight data pointing to the progression of tyre damage, for example, is also informing planning.
“It is this collaboration between technology, data and people that is absolutely key to this cycle we now see of more safe productivity garnering more safe productivity.”