Kal Tire leads the way in solving the challenge of scrap mining tyres
When an earthmover tyre reaches the end of its life, for many mines, the only option is to stockpile. Several years ago, Kal Tire’s Mining Tire Group set out to help customers solve this enormous environmental challenge, and that has led to a solution at the top of the recycling hierarchy gaining attention throughout the mining industry.
Kal Tire’s new OTR tyre recycling facility is the first of its kind in Chile, using thermal conversion to convert scrap mining tyres back to their base elements: oil, steel and carbon black. As mines place greater focus than ever before on ESG commitments, Kal Tire is excited about the potential to lead change and have a significant impact on scrap piles in Chile and around the world.
Creating a circular economy
Several years ago, Kal Tire began to explore mining tyre recycling options that could do more for mines and communities than traditional shredding. The project team asked, ‘How can we develop an effective way to recycle ultra-class tyres?’

Recycling giant earthmover tyres is complex: tyres can weigh 4 t and many mines are far from major centres. The project team also asked, ‘Could we aim to somehow create a circular economy by giving mines a way to reuse a tyre’s original materials?’
Just as the team was researching, Chile became one of the first countries to develop mining tyre disposal legislation. The need for a disposal alternative was great: Chile is home to six of the 10 largest copper mines in the world and nearly 500,000 t of scrap tyres. Kal Tire has been serving customers in Chile for decades, and so the legislation discussions became the impetus for Kal Tire to develop a mining tyre recycling solution that would first be implemented in northern Chile.
Significant research led the project team to thermal conversion recycling. It’s a unique process that uses heat and friction to induce a reaction that converts tyres to their base elements for viable reuse as high value chemical feedstock. Carbon black can be reused in batteries, plastics, pigments and paints. High quality tensile steel can be recycled in numerous ways. Oil can fuel generators, or it can be refined into alternative fuel for reuse in mine site equipment – creating a circular economy and the chance to have the greatest impact.
A practical, scalable solution comes to life
If the thermal conversion solution was clearly impactful, early on the team recognised the challenge of ensuring the solution would also be viable. They began the arduous process of developing the technology and building a 20,000 sq.m facility. Away from the drawing board, they had hundreds of conversations with customers and government to ensure the facility would meet all needs as well as the highest safety and environmental standards.
Throughout, Kal Tire commended the leadership of the government and the involvement of the mining industry, keen to operate in a way that is more environmentally responsible. As the facility’s wet testing approached, one of Kal Tire’s longstanding Chilean customers provided 2,300 tons (2,087 t) of scrap tyres.
Finally, in the spring of 2021, the first reactor’s full load tests were underway and were successful: the equivalent of five 63 in tyres were converted into 6,500 litres of alternative oil, 4,000 kg of steel and 8,000 kg of carbon black as well as enough synthetic gas to fuel the plant itself for seven hours.
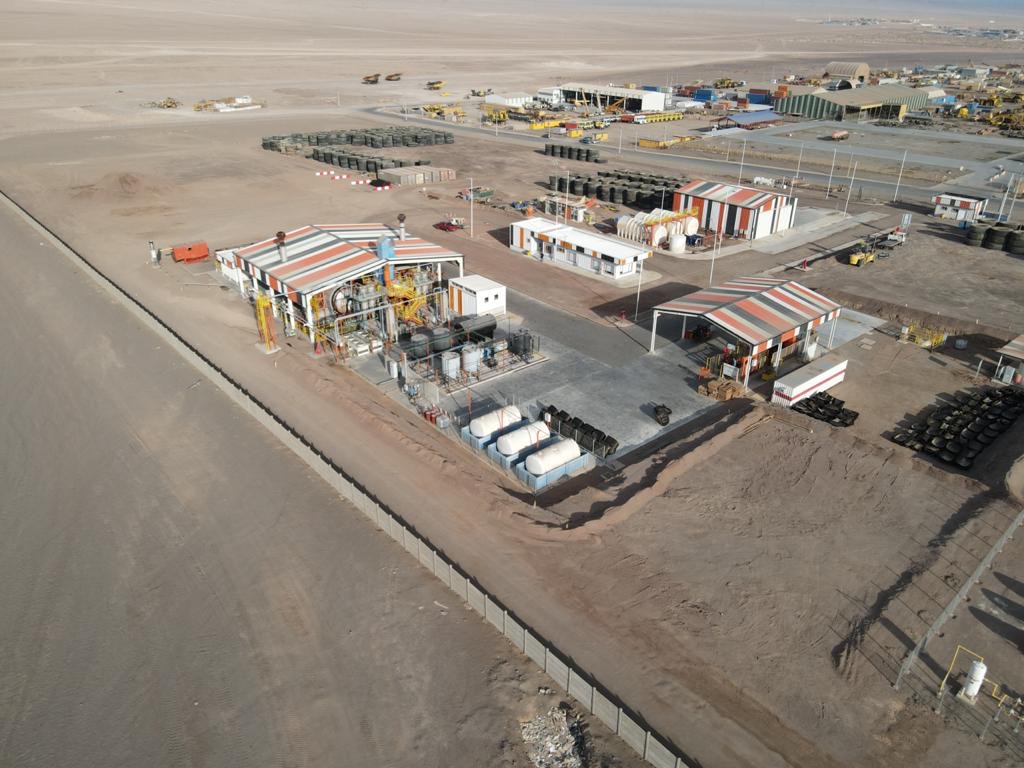
At full production, the plant will recycle five 63 in tyres or 20,000 kilograms a day; if the plant runs a minimum of 250 days of the year, that’s 5 million kg or 1,250 earthmover tyres in a year.
Now, as Kal Tire begins to recycle Chile’s decades of stockpiled scrap tyres, the entire mining industry is placing far greater focus on ESG commitments. As this solution is fully scalable, Kal Tire is now exploring opportunities to bring this technology to customers in other countries.
With stockpiles of scrap tyres in all of the world’s mining regions, the solution has the potential to transform one of the mining industry’s greatest environmental challenges into one of its greatest opportunities to operate sustainably and make an impact.