TAKRAF Group: 300 years of innovation serving the mining industry
2025 marks an important milestone for TAKRAF Group as it celebrates its 300th year anniversary, a longevity that in any industry is outstanding but which is particularly so in the complex and challenging mining environment.
Having evolved from a small but innovative iron hammer mill, established in what was in 1725 the Kingdom of Saxony, TAKRAF Group is today a major global operation providing innovative technological solutions to the mining and associated industries. With a presence in 14 countries on six continents, it designs and supplies innovative systems and technologies across the bulk material handling and surface mining value chains. In addition, its DELKOR brand provides a suite of liquid/solid separation and wet processing equipment that is specifically designed to meet the needs of the mining industry and enhance environmental sustainability.
Serving unique client needs
TAKRAF Group’s 300-year-old portfolio includes many of the mining industry’s milestone projects, including the world’s most powerful conveyor system. Building on this track record, current work features major projects such as the supply of an integrated In Pit Crushing & Conveying (IPCC) and material handling system for the Simandou iron ore complex in Guinea, one of the largest orders in the group’s history. In Mauritania, work is continuing on a contract from Societe Nationale Industrielle et Miniere (SNIM) to supply a complete iron ore crushing, screening and material handling system, along with a train loading station, for the F’Derick project.
Over the past year, TAKRAF Group has augmented its order book with new awards, covering both technology supply projects and aftermarket contracts, demonstrating its flexibility to meet the unique needs of its client base and support its products over their life cycle.
For example, a contract awarded this year covers engineering and supply of a conveying system for the Ujina growth copper growth project in Chile, the main objective of which is to increase the capacity of the concentrator plant. The contract awarded by Compañía Minera Doña Inés de Collahuasi SCM comprises design and supply of three advanced conveyors to seamlessly connect a relocated crushing station to the mine’s existing conveyor network. This equipment was supplied some 20 years ago by TAKRAF Group and has operated to exceptional standards of reliability since then under challenging operational conditions at an altitude of 4,535 m.
In South Africa, TAKRAF Group participated in a backfill project to supply a new extendable conveyor and to transfer an existing shiftable conveyor and spreader. Designed for a final length of 2,082 m, the conveyor initially saw only 615 m installed during this project. To address unstable ground conditions, the structural design takes into account that the conveyor is installed on previously backfilled material. As for the tail drive station – which houses 4 x 500 kW of installed power – its structure features a unique jacking mechanism that allows height and level adjustments in the event of ground settlement.
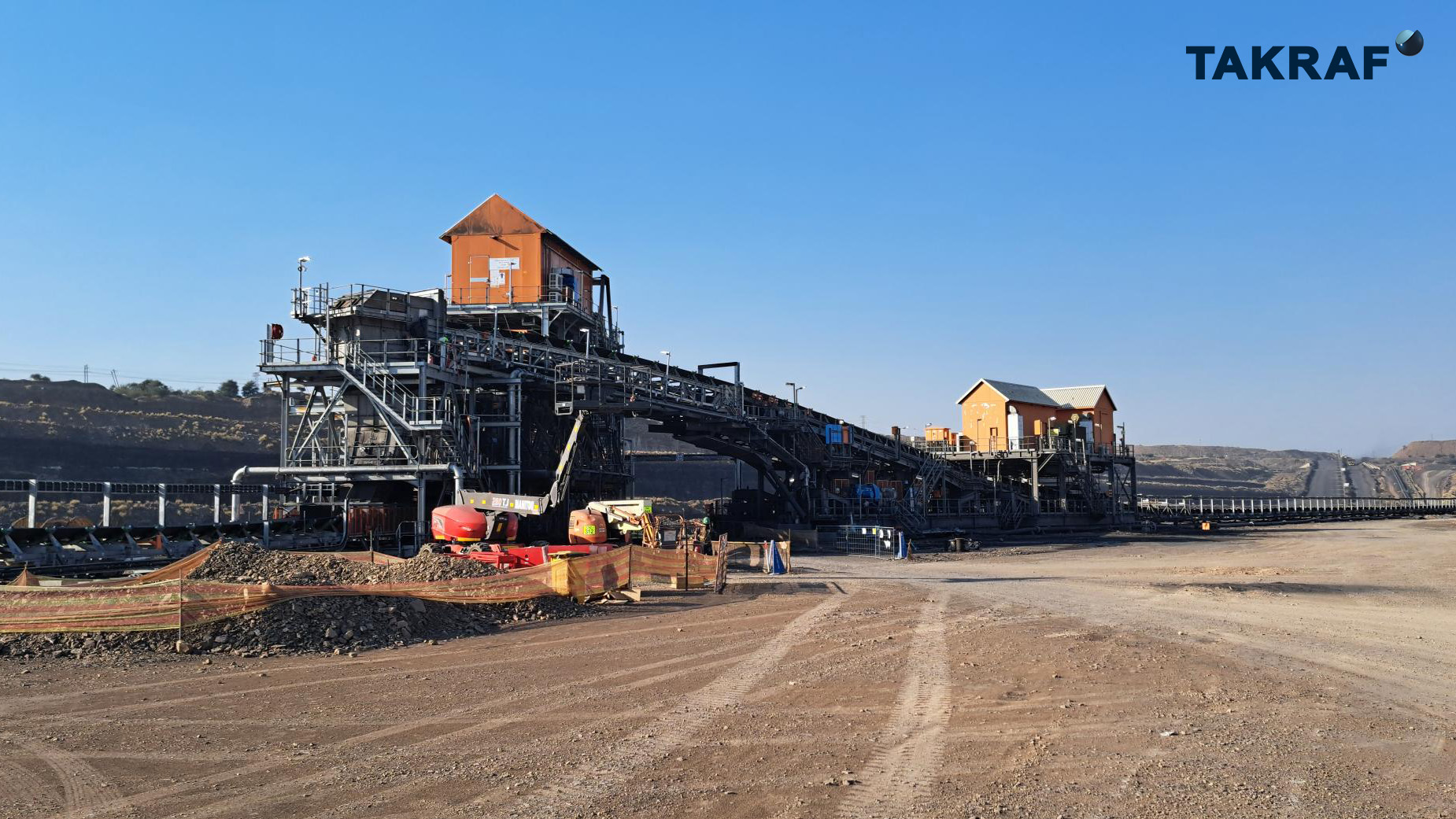
Full product lifecycle support
TAKRAF Group offers customised maintenance and refurbishment solutions ranging from continuous condition monitoring, spare parts supply and on-site repair support to major repairs, including complete refurbishments as an alternative to the purchase of new equipment, as well as equipment relocation.
In addition to supporting its own products, TAKAF Group services equipment supplied by other OEMs, as demonstrated in a recent project to replace the boom on an ash spreader at a power plant in South Africa. The 1,200 t/h spreader machine was originally installed more than 40 years ago by another OEM. Despite a number of project challenges, including the fact that the original drawings were not available, TAKRAF Group replaced the 31.5-m-long spreader boom in less than four months from contract award. The bespoke design included several improvements to the original design to ensure ease of installation and maintenance.
TAKRAF Group also continues to see good demand in India, with the award of four new orders for the revamping and maintenance of various Bucket-Wheel Excavators (BWEs) for one of the country’s largest lignite and power producers. TAKRAF Group’s collaboration with this company dates back more than 30 years. Two of the orders concern the major revamping of the mechanical and electrical portions of one 1,400-litre BWE and two 700-litre BWEs for other OEM supplied equipment to extend their operational life. The remaining two orders are maintenance contracts (mechanical and electrical, respectively) to reduce downtime and ensure equipment availability.
In Canada, TAKRAF Group was recently awarded two major aftermarket support contracts, covering relocation of a previously installed 850 t TAKRAF Crushing Plant and replacement of a head chute and back stay for a ship loader originally commissioned by another OEM.
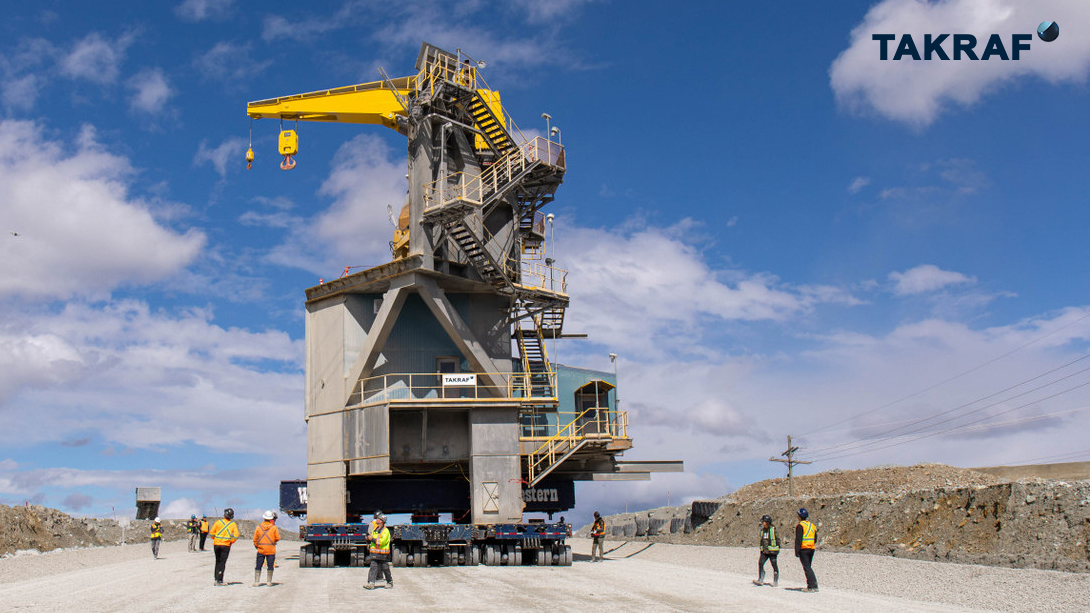
Dewatering equipment for environmental sustainability
The integration of DELKOR, a pioneer of liquid/solid separation technology, into TAKRAF Group in 2014 was a major development for the group in enhancing its capability to provide its client base with environmentally sustainable solutions. Among others, DELKOR’s dedicated dewatering products, such as thickeners, belt filters and filter presses, reduce the need for fresh water, improve water recycling rates and minimise waste.
As an example, a DELKOR Paste Thickener in operation at a major Indian steel manufacturer to treat iron ore tailings has resulted in significantly reduced water usage, an important environmental benefit in this water-stressed country. The 15-m-diameter paste thickener was ordered to increase water recovery within the process plant and increase the life of the existing tailings dam. With the installation of the paste thickener, process water recovery has increased to between 78% and 83% within the plant, which has, in turn, resulted in a significant reduction in the plant’s freshwater intake.
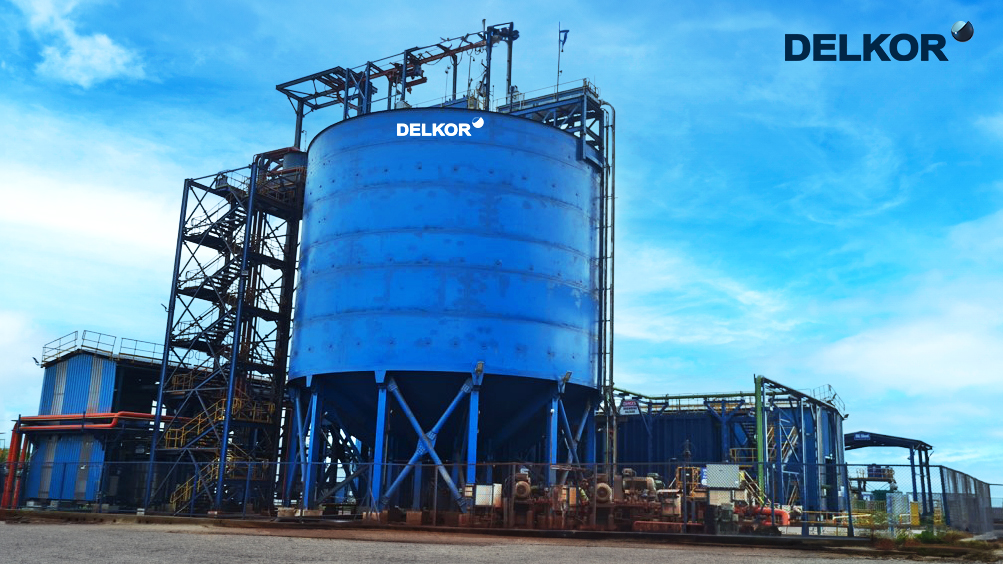
Other DELKOR equipment commissioned in recent years includes three 110 sq.m horizontal belt filters for a major fertiliser plant expansion project in Kazakhstan and two horizontal vacuum belt filters supplied for cobalt and copper operations in the Democratic Republic of Congo (DRC). Both latter filters were designed to achieve maximum recovery of water and produce a drier filter cake.
A major order for four 40 sq.m Belt Linear Screens (BLS) for a gold project in Australia followed a previous installment of several smaller belt linear screens at the client’s plant. The DELKOR BLS is the result of extensive test work to tackle a critical issue in gold processing by effectively removing trash material from process slurries.
In line with TAKRAF Group’s commitment to ongoing research and development, the DELKOR BQR Flotation Cell has seen major enhancement in recent years, with the introduction of the MAXGen mechanism to provide superior metallurgical performance. Not only does this mechanism assist in maximising metal recovery, but it can also result in fewer cells being required, with significant capex and opex benefits.

Following the success of its first commercial application in 2021, the new generation cell is in high demand across a range of commodities. Orders have included 14 DELKOR Flotation Cells supplied to a platinum project in South Africa, 11 units supplied to two gold mines, six cells for a nickel restart project in Australia 12 for a fluorspar processing plant in Spain and five for the processing of iron ore in Honduras.
300 years of innovation
Founded by the remarkable Benedicta Margaretha von Löwendal, TAKRAF Group’s forerunner, the iron hammer mill, from which Lauchhammer derives its name, grew exponentially over time, contributing major milestones to Germany’s industrial history. These included, in the 19th century, high-rise and iron bridge construction and the start of fabrication of overburden and lignite mining equipment. In the early 20th century, the first overburden conveyor bridge was supplied, followed by fabrication of the first three BWEs. The 20th century also saw the first 60 m moveable overburden conveyor bridge, for the Welzon Sued lignite mine, and the world’s largest bridge complex, the 60 m overburden conveyor bridge in the Klettwitz-Nord open-cast mine, both in Germany.
At the turn of the century, the longest conveyor for its time was supplied, to be followed in subsequent years by the development of TAKRAF Mobile Conveyor Bridges for stacking and reclaiming, the TAKRAF Mobile Crushing Plant, the double-roll crusher for oil sands and sizer technology, including the TAKRAF X-TREME Class Sizer range for hard-rock processing. A contract for the world’s most powerful conveyor system was awarded in 2015, a project which features the application of gearless drive conveyor technology. This was followed by development of High Pressure Grinding Roll (HPGR) technology for specific comminution requirements and supply of the first Dry Stack Tailings (DST) system for the environmentally friendly and safe disposal of tailings.
Innovation out of tradition – It pays to talk to a specialist!