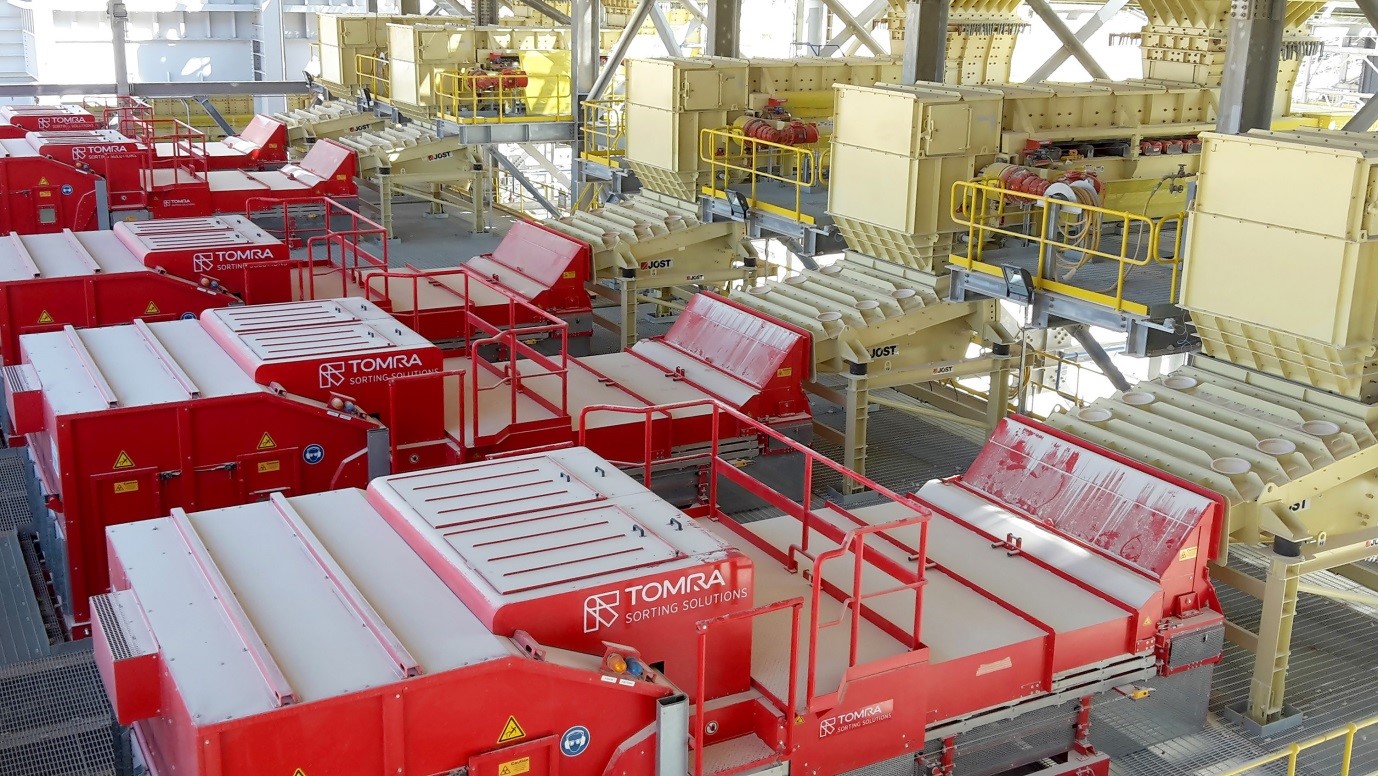
Sensor-based solutions specialist TOMRA Sorting Solutions is officially launching the latest upgrade in its ore sorting equipment range – the TOMRA COM XRT 2.0 – with features including higher belt speed and design capacity, as well as a heavy duty mining design and better accessibility for maintenance work.
According to TOMRA Sorting Mining Product Manager Ines Hartwig, the improvements in the new model are based on the successful track record of the TOMRA COM Tertiary XRT sorters on multiple sites across six continents.
“Over recent years, our sorters have notched up more than half a million operating hours under harsh conditions ranging from arid deserts to arctic environments, with both wet and dry feed,” says Hartwig. “The TOMRA COM XRT 2.0 is our flagship machine that will deliver significantly increased productivity to the resources sector.”
“Separation performance is central to the value added by these machines,” says TOMRA Sorting Mining Business Development Manager, PhD. Christopher Robben.
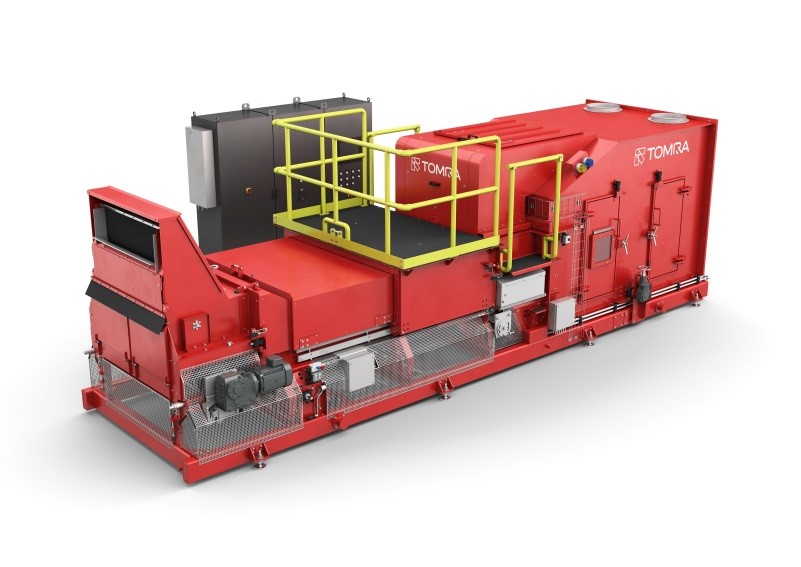
“The higher the separation efficiency, combined with more tonnage and improved uptime, the more value is added to the customer’s mining and processing operation,” says Robben. “The higher capacity means fewer sorters will be needed to do the job, reducing the amount of auxiliary equipment required to charge and discharge; ultimately resulting in a smaller overall footprint with less steel work. Efficient and high-volume separation is therefore a lever to reduce the total capital and operational expenditure of a sorting plant.”
Key features of the upgraded design include increased wear resistance and component lifetime, with improved mean time between failure. The mechanical platform of the TOMRA COM XRT 2.0 was also redesigned for safer, simpler, quicker and more ergonomic maintenance, by providing easier access to all relevant components.
“The separation chamber, in-feed chute, belt and air system components are all easy and quick to access, making the maintenance stops more efficient and giving the unit high availability,” Hartwig says. “Modular wear components also enable safe and ergonomic manual exchange in the shortest possible time.”
She highlights the increased speed of the belt from 2,7 to 3,5 metres per second, as well as the more powerful X-ray system which allows sorting of particle sizes due to better X‑ray penetration. With higher levels of belt occupancy, facilitated by improved data processing, the particle size of the feed can also be increased, thereby raising the machine’s capacity and creating a new industry benchmark.
The separation chamber, in-feed chute, belt and air system components are all easy and quick to access, making the maintenance stops more efficient and giving the unit high availability,” Hartwig says. “Modular wear components also enable safe and ergonomic manual exchange in the shortest possible time.”
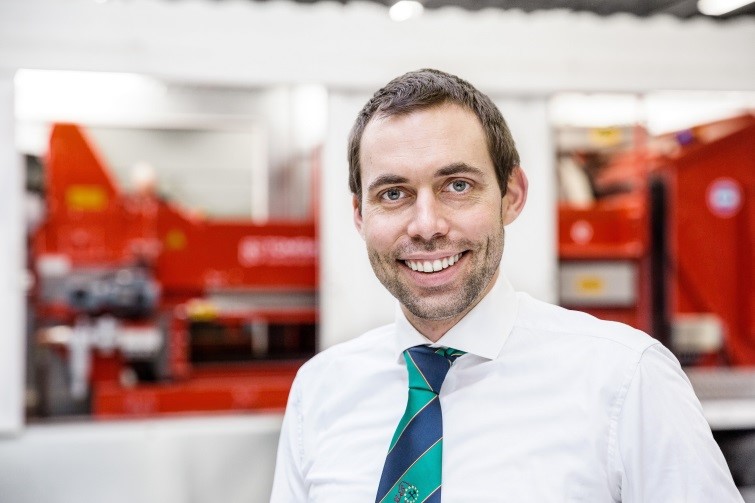
Double delivery
Depending on the material, the TOMRA COM XRT 2.0 can accommodate up to double the maximum size of the previous TOMRA model – from 60 MM to 80 mm on the COM Tertiary XRT to between 100 mm and 125 mm on the latest upgrade. This improvement translates directly into increased capacity at a ratio of 1:1.
“The result is a small plant footprint and low capital costs for mineral treatment projects, which translates into the lowest specific operating costs per tonne,” says Hartwig. “The higher capacity makes the TOMRA COM XRT 2.0 a particularly valuable proposition for larger mines, as it significantly cuts down the number of machines required. This economises on both capital and operating costs.”
The ejection system is highly selective, using data processing in combination with highly responsive pneumatic-valve ejectors. Developed in-house, TOMRA’s proprietary data processing pipeline, from sensor through image processing to the valve control boards, has several special features and filter mechanisms which allow precise control of the valves.
The system’s energy efficient design means that it requires only about half of the energy for compressed air when compared to conventional sensor-based ore sorting systems. Data on the separation efficiency also shows a low misplacement of waste-to-ore or ore-to-waste.
Hartwig emphasises the collective experience behind the development of TOMRA’s technology, including the vital feedback received from partners and customers throughout its installed product base.
The end-goal is to keep downtime as low as possible, so the maintainability and accessibility of the main components are also specially adapted for applications in the mining sector, keeping productivity and availability high.
“All the experience that we gain in monitoring operating mining installations are incorporated into our new mechanical designs,” she says.
“We learned early on, for instance, that sorters made for the recycling sector do not necessarily fit the purposes of mining processes. The higher tonnages and abrasive materials running through the sorter mean that the design needs to be more robust and must include increased wear protection.”
“Every part of the TOMRA COM XRT 2.0 which is in direct contact with the material is now wear-protected, and the tailormade wear protection is easily exchangeable,” she says.
The company’s prototype was designed to withstand the harsh demands of underground mining conditions, while still operating at a high capacity-to-volume ratio.
Design development on the new model dates back to 2015, when TOMRA Sorting Solutions participated in the European Union-funded I2Mine project to help realise the concept of an invisible, zero-impact underground mine.
According to Robben, a pilot installation at the New Boliden mine in Sweden showed that TOMRA´s sorting solution could lead to an increased productivity of 12%, while removing low grade material before truck transport and milling operations.
“This directly reduces specific energy consumption and carbon emissions for both grinding and transportation; a significant contribution to the I2Mine objectives and for the deep underground mine of the future,” he says.
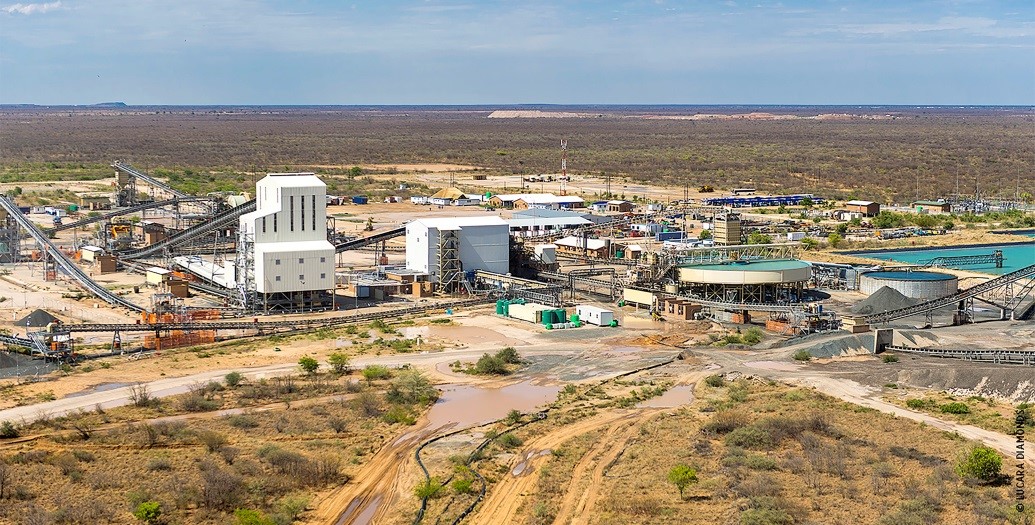
Hitting milestones
Since proving this ore sorting technology, the company’s milestones have included the installation and operation of its 1,850 tonne per hour sorter feed at Ma’aden Phosphates’ Umm Wu’al project in Saudi Arabia, and its 1,000 tonne per hour sorter feed at Karowe Diamond mine in Botswana. This is in addition to several smaller units in portable and containerised configurations in many different countries. Apart from the different climatic conditions which must be endured, these machines sort a variety of minerals from copper, iron ore and coal to industrial minerals, chrome and diamonds.
“The Umm Wu’Al project, one of the largest integrated phosphate fertiliser facilities in the world, is also the largest operating sensor-based ore sorting installation,” Robben says. “This makes it an important reference site for the TOMRA COM XRT 2.0 machines, which are employed in the plant’s silica rejection stage.”
The plant is part of the Waad Al Shamal phosphate project, a joint venture between the Saudi Arabian mining company Ma’aden, the US-headquartered company Mosaic, and Saudi petrochemical giant SABIC. The Umm Wu’al phosphate project is part of the development of a new industrial city in the north of the country. The plant is capable of processing 13,5 million tonnes of raw material per year, which can be sorted by just nine of TOMRA’s COM XRT sorting units, facilitated by each unit’s operational width of 2,4 metres.
“After extensive test work, Ma’aden came to the conclusion that TOMRA’s COM XRT sorters would be the most beneficial solution for its new $560 million processing plant at Umm Wu’al,” Hartwig says. “The sensor-based ore sorters at Umm Wu’al sort more than 70 per cent of the run-of-mine material by removing flint stones from the phosphate in order to reduce the silica content; by removing this hard waste material, the downstream process can be significantly down-sized. This installation removes more than 90% of
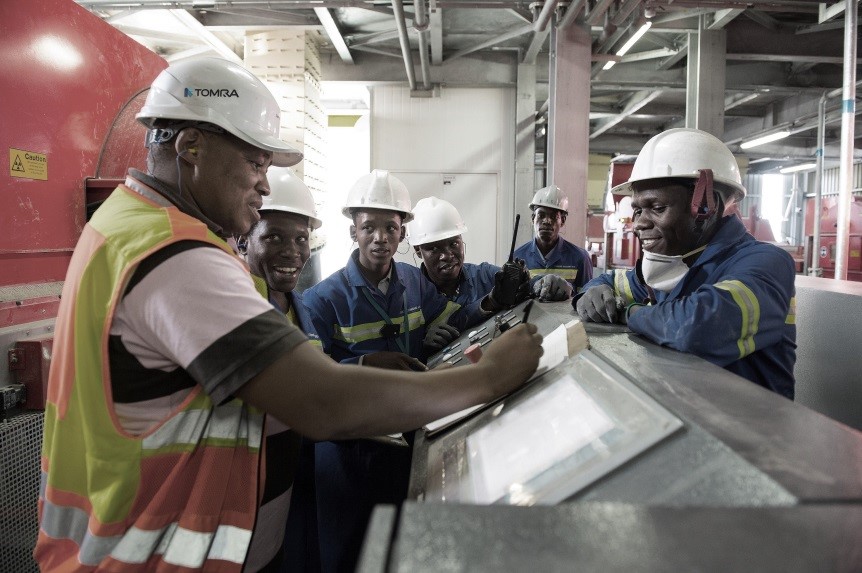
the chert in the +9 mm fraction, which represents 50% of the plant feed, before the phosphates are fed to the milling and flotation circuit. It considerably improved the mill performance by reducing the consumption of energy, water and chemicals per ton of final product, which was all achieved with a smaller sorting plant footprint.
At Lucara Diamonds’ Karowe mine in Botswana, two TOMRA COM XRT 2.0 /1200 models are installed in the mega-diamond recovery (MDR) circuit located directly after the primary crusher and ahead of the process plant. The MDR circuit treats material in the size range between 50 mm and 120 mm.
“This maximises the upfront recovery of exceptional diamonds prior to the comminution processes where diamond damage may occur,” Hartwig says. “The machine has proven itself through its high availability throughout its first year of operation there.”