Orica’s Cyclo™, a solution combining the company’s emulsifier technology with used oil processing technology to transform mine-site used oil for application in explosives, is off to a fast start with the first automated containerised system recently successfully commissioned in Ghana.
Cyclo is an example of Orica’s strategic focus on optimised resource use through circularity, it said in its recently released annual report.
While used oil/diesel blends have been utilised in process fuels for more than 15 years, the technique requires tight quality control and regular testing when used to manufacture emulsions, the company said. “As a result, it has only been feasible at sites with access to external laboratory services.”
To service a broader range of customers, Orica has partnered with CreatEnergy to develop a standalone, on-site solution to treat used oil to the quality required for emulsion manufacture.
Orica initially scheduled Cyclo for market introduction in late 2022, but it scaled and sped up development and production plans to support customers’ operations and curtail material supply disruptions brought about by COVID-19.
“Our first automated containerised used oil recycling system, Cyclo, was successfully commissioned recently in Ghana, Africa,” Adam Mooney, Vice President of Blasting Technology, said. “We are working to gradually commission further units across more customer sites in the coming months, including in Papua New Guinea and Senegal.”
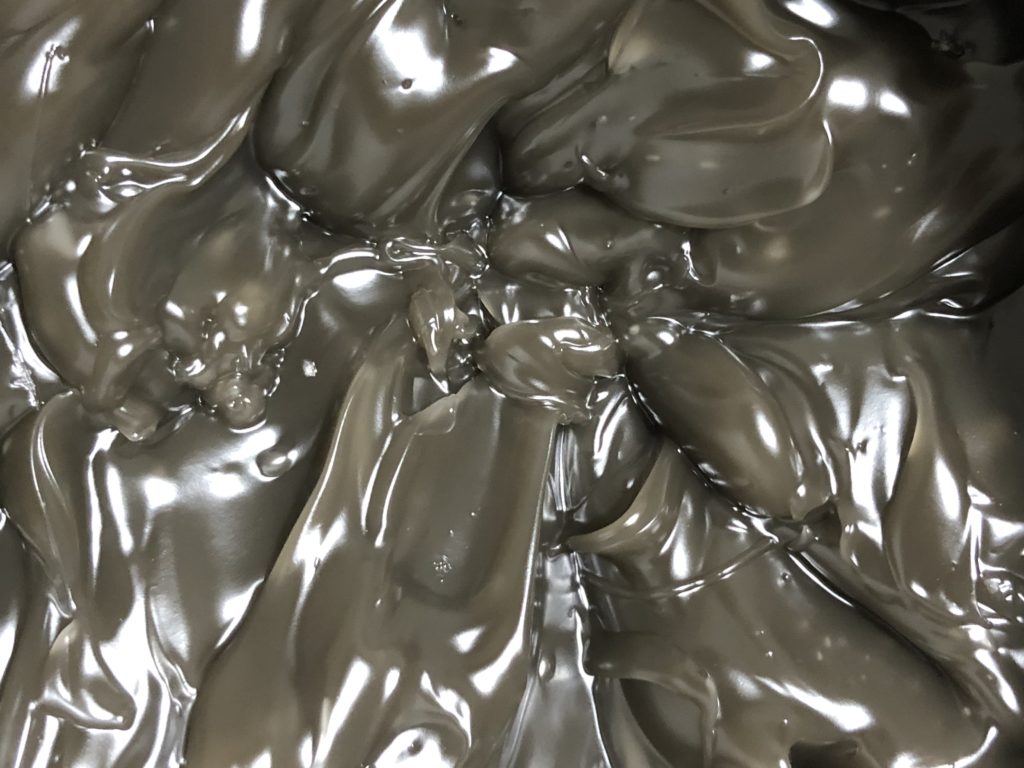
Over 33,000 litres of used oil has been processed to date through the initial Cyclo service, according to Mooney, who explained: “This is a modest quantity as the Cyclo unit was only commissioned remotely in recent months due to COVID-19. In a year, this mine is forecast to reduce their diesel consumption by approximately 250,000 litres.”
Mooney told IM that its used oil recycling technology is designed to support customers’ remote operations where Orica’s site-based emulsion plants are available.
“The key difference in the Cyclo service with existing offers in the market is that the containerised processing system is fully integrated into our on-site emulsion plants, enabling the used oil from the mine to be directly recycled without leaving the site,” he said. “The processing unit guarantees used oil quality to the standard required for emulsion manufacture by removing potential contaminants and, when combined with proprietary Orica emulsifier technology, guarantees finished bulk product quality.”
These installations will, the company said, reduce the annual diesel consumption for explosives manufacture for customers, depending on bulk product consumption, by some 250,000-800,000 litres per year per site when operational, delivering an environmental and commercial benefit to customers. On top of the obvious diesel consumption benefits, the solution will reduce truck movements through local communities and the associated logistical challenges and risks, particularly for remote operations.
A version of the Cyclo system to suit Arctic conditions (eg in Russia and parts of Asia) is currently being designed and will be operational in 2022, Mooney added.