Among a long list of new products, digital solutions and displays Sandvik plans to introduce at North America’s largest construction tradeshow, CONEXPO-CON/AGG 2023, in Las Vegas, USA, is the Ranger™ DX910i, the company’s latest flagship top hammer surface drill rig.
Sandvik will showcase some of its newest innovations in surface drilling, rock tools, stationary crushing and screening and parts and services at the event, which runs from March 14 to March 18.
The Ranger DX910i is being launched together with new drilling tools. The shoulder-driven curved thread systems CT55 and CT67 increase productivity and reduce fuel consumption, according to the company.
The Ranger DX910i on display will be equipped with the new high-power rock drill RD930C, which expands Ranger DX910i’s hole size range beyond existing DXi rock drill options.
The company will display its electric concept surface drill rig, which demonstrates advanced technologies that will be featured on future Sandvik surface rigs to support more sustainable and energy-efficient drilling. It will also showcase its Leopard DI650i, a surface drill simulator and the RockPulse system for optimising Ranger drilling results.
The OEM will display its latest rock tools offerings at CONEXPO-CON/AGG, including the Tundo™ RH650 down-the-hole hammer, Sandvik Alpha™ 340 top hammer drilling tools, which feature an entirely new asymmetric thread, as well as the LT90 top hammer drilling tools. The company will also highlight its Carbide Recycling Program for recycling customers’ worn carbide tools, aimed at improving sustainability across the value chain.
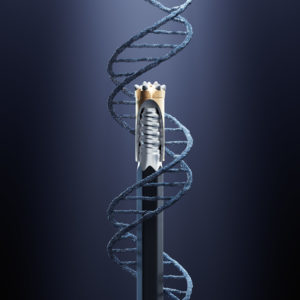
The technologically-advanced Sandvik CH865i mid-range cone crusher will anchor the stationary crushing and screening display at the event, which will also feature SAM by Sandvik, the ever-evolving “always on” digital assistant to support operational excellence in crushing and screening plants, as well as the next generation Sandvik Automation and Connectivity System (ACS-c 4.3) for optimising crusher performance, the company says. Sandvik will also showcase its Sandvik CV217 vertical shaft impact crusher as well as screening media and wear protection.
Sandvik’s parts and services exhibit at CONEXPO-CON/AGG will include an interactive display introducing My Sandvik Productivity for Boom Drills, a telematics solution providing easy-to-read dashboards for faster, fact-based decision making, it said. Exhibit visitors can also l experience a live demo of Sandvik’s Expert Off-Site, an on-demand web-based service that instantly connects customers with Sandvik experts remotely, minimising downtime costs typically associated with waiting for technical support, the company explained. Sandvik will also highlight its extended warranty solutions and comprehensive equipment rental offering.