A four-year collaboration between Orica and LKAB has resulted in the first production blasts using wireless initiation technology at the Kiruna iron ore mine in northern Sweden.
These blasts – charged in the middle of May and blasted in early June – are going some way to support LKAB’s safety, productivity and long-term automation objectives, according to Abhisek Roy, EMEA Head of Marketing for Orica.
It has involved an extensive amount of work to get to this blasting milestone, according to Ingemar Haslinger, Technical Services Lead Europe at Orica.
He explained: “It all started in 2018 when LKAB showed interest in our new WebGen™ wireless technology. They could see the benefits in both safety and productivity with the new way of producing the ore.”
This saw Orica go to site at the Kiruna mine in March 2018 to begin with a signal survey, testing if the company could obtain a good signal between the antenna and the in-hole receivers.
WebGen provides for groups of in-hole primers to be wirelessly initiated by a firing command that communicates through rock, water and air. This removes constraints often imposed by the requirement of a physical connection to each primer in a blast. The wireless blasting system not only improves safety – by removing people from harm’s way – but improves productivity – by removing the constraints imposed by wired connections.
It is, therefore, considered, a critical pre-cursor to automating the charging process.
To this point, WebGen has fired over 100,000 units in over 3,000 blasts globally across customer sites, Orica says.
At Kiruna, however, the process from testing to technology on-boarding was less than straightforward.
“In the area of the mine where the signal survey was completed in 2018, it was discovered that the signal could not penetrate the magnetite ore at all,” Haslinger said. “This was the first time we had encountered this and was a setback for Orica and LKAB.”
At that time, Orica did not have the localised field equipment or advanced diagnostic tools to diagnose the antenna issue, making it difficult to ascertain the root cause.
“We had to go back to our global WebGen specialists and try to understand why this was happening, which we were successfully able to do,” Haslinger said.
After dedicated work from the global team, Orica went back to Kiruna in September 2020, looking to replicate the signal survey from 2018 and use its advanced diagnostic tools to measure the antenna performance and output.
“We also had the opportunity to test the signal behaviour in the holes, as well as measure the rock properties around the antenna and the in-hole receivers,” Haslinger added.
The survey proved successful, explaining why the signal could not go through the orebody. This allowed the global WebGen team to start developing solutions to overcome the signal problem, which it was able to do in short order.
In December 2020, the Orica team was back at the underground iron ore mine to test the new solution.
“The first trials with the new solution showed positive results and the global team continued to develop that further,” Haslinger said. “In May 2021, we tried the solution in many different conditions and applications to be sure that it would work in the mine. These trials gave us a lot more knowledge about the environment and how the new solution worked.
“In 2022, we were ready to test the system in active mine operations and it has been an extensive amount of work to get us to that point.”
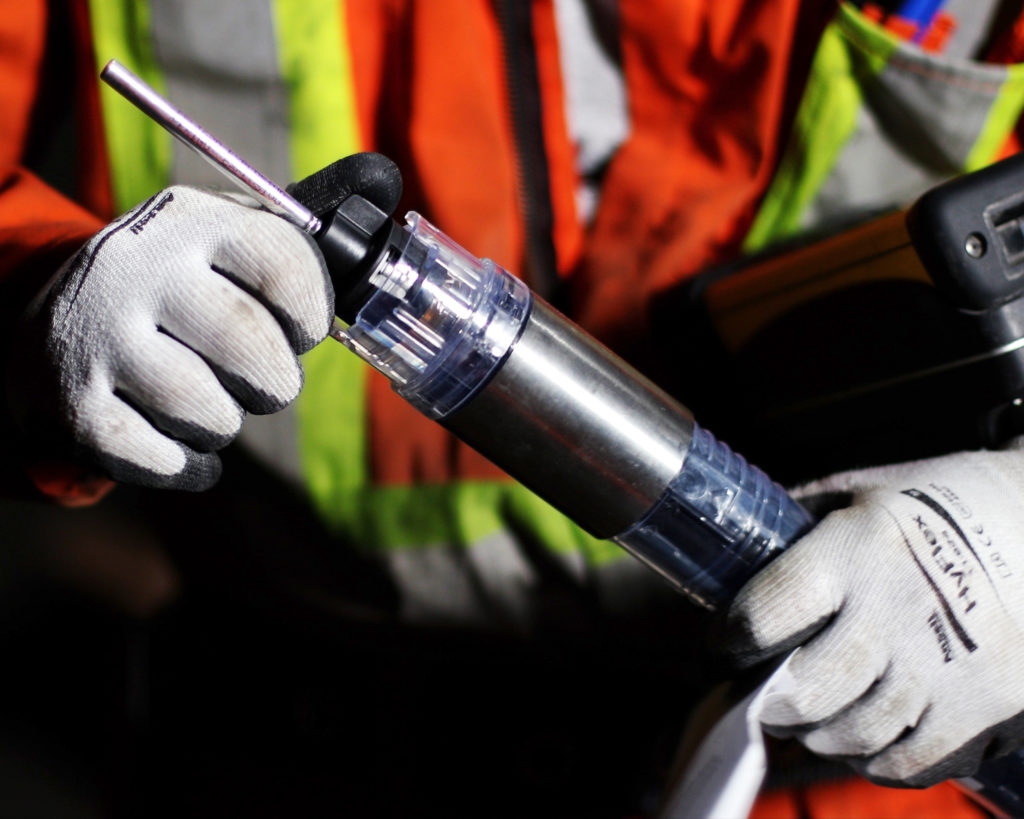
Michal Gryienko, Engineer at LKAB in Kiruna, said the first two production rings were charged using WebGen in the middle of May before blasting occurred in early June. This is one of the benefits of the system, with the wireless primers able to sit dormant in the blasting profile for around 30 days prior to blast initiation.
“The results look good so far,” Gryienko said. “In total, we will blast five production rings, and the final three are planned to be blasted in September.”
Among the benefits Gryienko highlighted were the reduction in risk associated with hole priming and the possibility of detonating more blast holes due to the ability overcome damaged or unstable blasting applications.
Orica’s Roy said the collaboration between the two companies has been “fantastic”.
“Despite the challenges around transmission of signal across the magnetite orebody that is a prerequisite for a successful wireless initiation, both companies have worked as partners for the last four years, finding practical and creative solutions,” he said.
“This hopefully is the start of a long-term sustainable wireless blasting solution that supports LKAB’s safety and productivity objectives and long-term automation goals.”