Ore sorting has been shown to provide both economic and environmental benefits, but many mines are not yet fully utilising this technology, according to HPY Technology.
Yet, the company’s ore sorting machines are providing a breakthrough solution for Fankou, one of Asia’s largest lead and zinc mines, resulting in an annual revenue increase of around $9.22 million.
Located in Renhua County, Shaoguan City, Guangdong Province, Fankou is owned by Shenzhen Zhongjin Lingnan Nonfemet Co Ltd. The mine has been producing lead and zinc for over 60 years. However, with new underground mining processes, such as vertical crater retreat and large blasting, more waste rock is being introduced into the crushing, grinding and flotation processes, resulting in higher production costs and energy consumption.
Furthermore, under the “zero waste” target set by the Environmental Protection Law of China, Fankou’s tailings pond needs to be closed by 2025. As of 2018, the mine’s annual processing capacity was 1.5 Mt, with 600,000 t ending up in the tailings pond. In addition, Fankou’s waste rock piles had reached approximately 2 Mt. With the continuous addition of around 200,000 t/y of waste rock, these piles grew larger. With the pressure to meet the zero waste target, Fankou was under pressure to make a change.
In 2017, Fankou conducted exploratory tests of sensor-based ore sorting machines with Ganzhou HPY Technology Co Ltd. The result of the initial tests showed promise and addressed the problems the mine was beginning to face, according to HPY Technology. As a result, Fankou decided to add HPY Technology’s ore sorting machines to the industrial design plan of their mineral processing plant in 2018, and HPY Technology’s machines were officially added to the plant in 2019.
The Fankou lead-zinc mine currently produces about 1.4 Mt/y of ore, and it is expected that more than 105,000 t of waste rock will be pre-rejected from the raw ore throughout the year. Ore sorting technology can discard a large amount of waste rock from the raw ore before it is fed into the flotation system, reducing the amount of waste rock entering the mill and saving on electricity costs.
Fankou’s mineral processing plant uses four Classic Series P60-X1400 ore sorting machines. The machine processes the particle size range of +12-90 mm, which accounts for about 50% of the raw ore. This accounts for 2,600 t of ore, rejecting 400-500 t/d of waste rock. After pre-concentration, the lead and zinc content in the waste rock are below 0.3%, and the sulphur and iron content is below 3.8%. Therefore, the ore sorting process enriches the ore grade by 1.08% for lead and zinc and 2% for sulphur and iron.
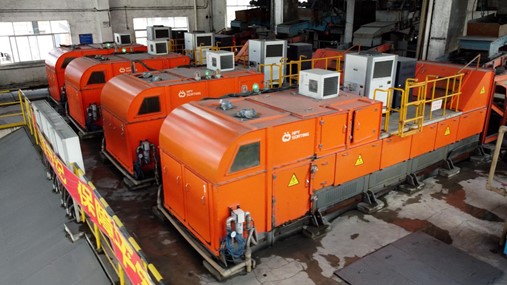
After sorting the waste rock from the raw ore, this waste rock can be sold as construction aggregate to bring further economic benefits to the Fankou mine. This has also seen the amount of tailings decrease and the service life of the tailings pond extend significantly, resulting in remarkable energy savings and consumption performance, while also enhancing the mine’s societal value, HPY Technology says.
Mr Wang, Project Manager of Fankou Mineral Processing Plant, said: “We are proud to be one of the world’s first lead and zinc mines to utilise ore sorting fully. We see significant economic benefits for using HPY Technology’s ore sorting machine, especially for low-grade mines. China has huge lead and zinc ore reserves, the second largest in the world. But the grade of the deposits is generally low, with many poor and few rich ores. The average grade is about 1.5% for lead and 2.5% for zinc. Reserves with a grade below 5% account for more than 90% of lead ore, and reserves below 8% account for more than 85% of zinc ore. We hope to continue contributing to the mining industry’s progress and are willing to recommend HPY Technology’s ore sorting machine to our peers.”
The Classic Series used in Fankou’s mineral processing plant is a benchmark in the ore sorting industry, according to HPY Technology. This machine uses dual-energy X-ray technology, combined with high-speed air jets to sort ore from waste rock. The X-ray technology penetrates the ore and creates a grayscale image that distinguishes between target and vein minerals. This image is then processed by an artificial intelligence algorithm, which uses the information to accurately sort the ore and waste rock. The Classic Series has undergone numerous iterations, ensuring stable and efficient operation, HPY Technology says. It is currently the most widely used ore sorting machine in China’s mining industry, according to the company.
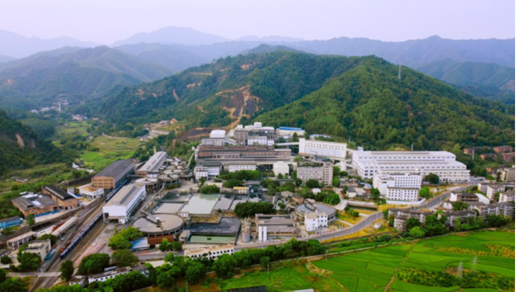
HPY Technology | Fankou lead-zinc mine, mineral processing plant |
|
Machine used | Four Classic Series P60-X1400 |
Processing capacity | 2,600 t/d |
Particle size | +12-90 mm |
Concentrated ore grade | (Pb+Zn) 12% |
Waste rock grade | (Pb+Zn) <0.3% |
Grinding grade | (Pb+Zn) increased by 1.08% |
Rejection rate | 16-17% |
Fankou’s mineral processing plant can save more than $2.9 million/y by using HPY Technology’s ore sorting machines, resulting in an annual profit margin of more than $7.8 million, considering the comprehensive benefits of increased plant capacity, tailings reduction and construction aggregate sales.
In addition to the four Classic Series P60-X1400 in the mineral processing plant, the Construction Materials Plant has three HPY Technology ore sorting machines to process the waste rock from the mineral processing plant and its existing waste rock piles. The waste rock is taken to the construction material plant for another round of sorting, with the remaining waste rock being used for construction aggregates. The three machines at the construction materials plant also process the 2 million cu.m of waste rock initially stockpiled in the tailings pond.
Mr Luo, Project Manager of Solid Waste Treatment, said: “In the past, we could only transport solid waste back to the shaft for filling. After using HPY’s ore sorting machines, we can now sort out all the ore from solid waste and recover the value of the resources. The remaining waste rock can be sold as construction aggregates, which is a win-win solution. Currently, we are also sorting waste rock that was stored before using HPY’s ore sorting machines. The ore grade is about 3%. Sensor-based sorting technology enriches the ore grade to 12-14%. Sorting results show that the rejection rate exceeds 95%. In the global mining industry, Fankou is one the first to successfully apply intelligent ore sorting technology in lead and zinc mines, achieving maximum resource value recovery and is great for the environment.”
According to Mr Luo, waste rock that was initially made into construction aggregates now yields more than 1,500 t/y of lead and zinc metal, which has been able to be recovered through the Construction Materials Plant. In addition, the ore sorting process reduces the waste rock’s sulphur content. This substantially improves the grade of the construction aggregates, increasing its sales price. As a result, the waste rock made into construction aggregates generates about $977,000/y in economic benefits. In addition, the recovered ore generates over $2.8 million/y in benefits.
Fankou has utilised sensor-based ore sorting to its full extent, HPY Technology says, using it during the comminution process to pre-reject waste rock to increase its lead-zinc ore grade. The company also sees benefits from pre-rejected waste rock in reduced costs in its grinding process. With pressure to control the amount of tailings, the pre-rejected waste rock lowers the amount of tailings entering the tailings pond to help the company in its aim of closing the tailings pond in 2025. In addition, sensor-based ore sorting has allowed the company to gain additional revenue through the recovery of lead-zinc from their waste rock piles, while also utilising these piles for construction aggregates. Overall, the introduction of ore sorting has allowed the company to expand its resource recovery. By pre-rejecting and enriching low ore grades, Fankou can now mine areas previously deemed un-mineable due to having low grade ore, allowing them to increase the processing capacity each year.
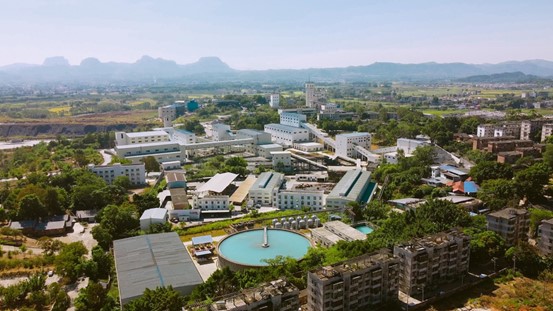
HPY Technology | Fankou lead-zinc mine, Construction Materials Plant |
|
Machine used | One Insight Series | Two Classic Series |
Concentrated ore grade | 12-14% |
Waste rock grade | Pb 0.04%, Zn 0.10% |
Concentrate recovery rate | Pb 96.76%, Zn 92.8% |
Rejection rate | 95% |
Enrichment ratio | Pb 9.68, Zn 9.28 |
Particle size | +10-50 mm |
The Insight Series used in Fankou’s Construction Materials Plant adopts a combined detection method comprised of a VIS HD dual-sided imaging system and X-ray technology, which can be customised according to the physical characteristics of different ores. The machine can collect the ore’s internal and external information simultaneously and with an AI algorithm, which can significantly improve the accuracy of ore sorting and better for sorting complex ores.
Compared with traditional ore sorting machines, which use a belt, the upgraded Insight Series utilises a vibrating feeder and short belt that leads to ore free fall, HPY Technology says. With the optimised mechanical design, the ore falls more evenly, avoiding ore overlap that affects recognition accuracy. In addition, the machine has various feeding widths (1,600 mm, 3,200 mm), which leads to processing capacities of 40-150 t/h (+10 mm-80 mm) to meet the needs of different mines needs during the beneficiation process.
As one of Asia’s largest lead and zinc mines, Fankou has taken steps to maximise the economic value of its process. Through the utilisation of sensor-based ore sorting, the company has seen significant increases in revenue and savings. Having worked with HPY Technology for over five years, Fankou looks to continue this partnership to further the research on the benefits of ore sorting machines. As HPY Technology continues innovating and revolutionising mineral processing, the benefits will only continue to grow, it says.
HPY Technology Co Ltd says it is a leader in the development and manufacture of ore sorting machinery, achieving excellent results in the ore sorting of tungsten, tin, antimony, lead, zinc, copper, molybdenum, gold, phosphate and over 30 other ore types, revolutionising the traditional mineral processing process and significantly promoting the technological progress of the global mining industry. With over 400 machines in use in over 100 mines, the company says it looks to continue revolutionising mineral processing.